Is there a better way to make a 180 degree pipe intersection? My attempt was just merging the two mesh together in boolean, but the intersection topology isn't good as well as the sharp corners.
Is there a better way to make a 180 degree pipe intersection? My attempt was just merging the two mesh together in boolean, but the intersection topology isn't good as well as the sharp corners.
Bear with me, I'm really new to Blender so trying my best.
But, the easiest and fastest way, is just like you're doing it. Fewer.
Step one, two similar pipes. Make sure that they align.
step two, Boolean, Union. Clean up wherever it messes up.
step three. Add the support loops.
step four. Subdivide/Turbosmooth.
Sides on the cylinder 6-8 sides. Match them up. And add the support loops.
Is there a better way to make a 180 degree pipe intersection? My attempt was just merging the two mesh together in boolean, but the intersection topology isn't good as well as the sharp corners.
Bear with me, I'm really new to Blender so trying my best.
But, the easiest and fastest way, is just like you're doing it. Fewer.
Step one, two similar pipes. Make sure that they align.
step two, Boolean, Union. Clean up wherever it messes up.
step three. Add the support loops.
step four. Subdivide/Turbosmooth.
Sides on the cylinder 6-8 sides. Match them up. And add the support loops.
Is there a better way to make a 180 degree pipe intersection? My attempt was just merging the two mesh together in boolean, but the intersection topology isn't good as well as the sharp corners.
You can also use Add Mesh: Extra Objects Blender addon. It can save you some time. It's an addon that is shipped with Blender.
Since we're on pipes/cylinders, I'm modelling after a reference that calls for the pipes to be at this angle, and I've connected them in a way I thought makes sense, but it creates a shading issue that I can't seem to fix. Here's the issue with wireframe and a mocap material to hopefully show it off better
I tried adding some very close edge loops to "constrain" the problem, and while it does fix the issue, I was wondering if there's a way to make the joint look more... natural:
I've checked all the pipe tutorials I could find, but none of them cover cylinders being connected at this angle, always 90 or 45 degree connections.
Since we're on pipes/cylinders, I'm modelling after a reference that calls for the pipes to be at this angle, and I've connected them in a way I thought makes sense, but it creates a shading issue that I can't seem to fix. Here's the issue with wireframe and a mocap material to hopefully show it off better
Hi, maybe a good way to make this pipe more appealing is something like this?
Since we're on pipes/cylinders, I'm modelling after a reference that calls for the pipes to be at this angle, and I've connected them in a way I thought makes sense, but it creates a shading issue that I can't seem to fix. Here's the issue with wireframe and a mocap material to hopefully show it off better
Hi, maybe a good way to make this pipe more appealing is something like this?
I don't know why it didn't occur to me to try a flat surface. The reference I'm using also isn't very clear on this pipe section, so I'm sure it also won't be an issue as well. Thanks!
I'm trying to model this radar antenna thing and while I have the base mesh prepared, the reference has the mesh hollowed wither certain faces on certain areas. I tried to make them with loop cuts, but they ruin the silhouette and shape of the mesh. Is there a better way?
I'm trying to model this radar antenna thing and while I have the base mesh prepared, the reference has the mesh hollowed wither certain faces on certain areas. I tried to make them with loop cuts, but they ruin the silhouette and shape of the mesh. Is there a better way?
Hey bud. I'm guessing it's also those ribs on the inside giving you trouble, so I included those here. One way to tackle this is to model it flat and straight, then bend it into the shape you want. Note that I didn't take the skewed part of it into consideration, nor the details at the top. I'm only trying to show you how to get the details in without messing with the curve. The important thing is that the curve needs a consistent amount and spacing of edges, or it will end up wonky like your result.
I want the wall thickness at 1mm and edgeloops at 1mm, so I start with a plane that's 38mm long, and with (Length-1=37) lines going through it. That leaves me with 1mm strips.
----- If you want the entire thing to have a skewed thickness like your ref, this is the time to add it in. I didn't add it in and it won't be shown. For 3ds max, a soft ramp FFD is all that's needed. -----
Then I plan to have a 1mm "ceiling" and "floor", so I add those in.
Then I want the internal strips to end 2mm above the floor, so I add that in, and their supporting edgeloops.
The point is to get this selection of polygons ready. This is the surrounding structure and the ribs within, all with 1mm edgeloops ready to go.
I shell that plane by 1mm to generate a back wall, then extrude those polygons by however much I want.
Two symmetry modifiers later and I have my final shape
One bend modifier later and I have the final shape.
I'm trying to model this radar antenna thing and while I have the base mesh prepared, the reference has the mesh hollowed wither certain faces on certain areas. I tried to make them with loop cuts, but they ruin the silhouette and shape of the mesh. Is there a better way?
Hey bud. I'm guessing it's also those ribs on the inside giving you trouble, so I included those here. One way to tackle this is to model it flat and straight, then bend it into the shape you want. Note that I didn't take the skewed part of it into consideration, nor the details at the top. I'm only trying to show you how to get the details in without messing with the curve. The important thing is that the curve needs a consistent amount and spacing of edges, or it will end up wonky like your result.
I want the wall thickness at 1mm and edgeloops at 1mm, so I start with a plane that's 38mm long, and with (Length-1=37) lines going through it. That leaves me with 1mm strips.
----- If you want the entire thing to have a skewed thickness like your ref, this is the time to add it in. I didn't add it in and it won't be shown. For 3ds max, a soft ramp FFD is all that's needed. -----
Then I plan to have a 1mm "ceiling" and "floor", so I add those in.
Then I want the internal strips to end 2mm above the floor, so I add that in, and their supporting edgeloops.
The point is to get this selection of polygons ready. This is the surrounding structure and the ribs within, all with 1mm edgeloops ready to go.
I shell that plane by 1mm to generate a back wall, then extrude those polygons by however much I want.
Two symmetry modifiers later and I have my final shape
One bend modifier later and I have the final shape.
Turbosmoothed isoline
Closeup
Thanks a lot. The radar part also has sloped sides that are difficult to create with a flat straight model. I used booleans to create the slopes on my attempt, but it doesn't seem like it would work well in your example. What do you suggest?
Thanks a lot. The radar part also has sloped sides that are difficult to create with a flat straight model. I used booleans to create the slopes on my attempt, but it doesn't seem like it would work well in your example. What do you suggest?
Maybe something like this will work?
You can adjust what part of mesh will bend using SimpleDeform modifier's Limits properties: I use an Empty object as the origin for SimpleDeform modifier to adjust how exactly mesh should bend.
To make slopes you can use the Lattice modifier. Assign a vertex group to specific vertices that you want to deform. Also set Interpolation: Linear in Lattice object's properties.
Of course, when you want to add more details, you might have to apply modifiers. It's not always possible to continue keeping it non-destructive.
HI I don't know how to deal with the line here. There are protruding things on this surface and a hole in the bending position. Is there any good way? Please help me. HI
For example, if you're planning to model those details out as part of a game asset creation process, then look into 'floaters' (Floating Geometry) otherwise search optimized hard surface or gun modeling techniques, there'll be options aplenty too choose from.
The best thing to do in this situation is to post your solution! Share with the community. There are likely to be others in a similar situation, and your solution will be appreciated.
Everything is fine, except this intersection here, you can see it's warping and causing shading issues:
I'm not quite sure how to fix this, i've tried modifiers, i've tried destructive. All i can figure is if i want the shape of the flat cutout off a circle that's going into a rounded shape, i may simply have to freeze the subd first, then extrude inwards and bevel last. Is it as simple as an order of operations or is tehre a topology issue here i'm not seeing?
Everything is fine, except this intersection here, you can see it's warping and causing shading issues:
I'm not quite sure how to fix this, i've tried modifiers, i've tried destructive. All i can figure is if i want the shape of the flat cutout off a circle that's going into a rounded shape, i may simply have to freeze the subd first, then extrude inwards and bevel last. Is it as simple as an order of operations or is tehre a topology issue here i'm not seeing?
Hi. I'm a noob so please take my advice with caution
If you increase the number of segments in your ring twice the crease will be much less visible:
I know there are real gurus on this forum, so probably someone will give better advice.
Now that I got the shape right, how do I get the end to bend like this with such dense geometry?
You can try to increase resolution of Lattice and then deform it:
After I press R to rotate the lattice vertices, I press Z to rotate only along the Z-axis. Unfortunately, the ScreenCast Keys addon does not register those keystrokes.
Thanks. But using a second lattice doesn't work too well as it warps a part of it in a bad way and reducing it to a single lattice or rearranging the lattices don't help. I there another way?
After asking a friend, I finally found a solution: -Apply the lattices that makes the end thinner and the one that bends the end -Choose a face that is rotated at a good angle before the rotations start falling apart -Add a transform orientation for the face on the top middle -Select an edge on the bottom loop if you have more loops -Make a face from that (lock the axis to X or Y when editing so the face`s orientation is consistent to that of the edge, which is where the transform orientation comes in handy) -Select the verts that come after that edge -Turn on snapping for face, set to active, and turn on project individual elements -Set the transform orientation to global -Go in orthographic top view -Snap the verts to the face on the Z vertical axis (Z in Blender and Y in other software) -Repeat the same steps for each loop -Done
Hello! I am still learning 3d Modeling. Since I model for 3d printing I have been using Booleans to make most of the details. I am trying to learn how to model them more 'properly' but I am having trouble maintaining the over all curves of the piece I am adding the details too.
The first picture is the lowest LOD and the second one is me trying to figure it out but its getting really messy and starting to lose the curve. The blue piece is one of the original Booleans. I work in Maya, All and any advice is appreciated!
If you're thinking of printing this, then I'd suggest a Shrinkwrap option in Maya under the Deform menu or just simply boolean / manually edit those insets correctly on a curved surface as previously illustrated a few pages back:
I'm trying to make the hinge on my model of these tank tracks. I followed a 3DS Max tutorial and tried doing it in Blender. the results were not good. Is there a better way to do this in Blender?
Update: I successfully created the shape I wanted, but because this will be duplicated many times over, it is too high poly for my PC to handle. Is there are more efficient way to make a tank track like this?
Update: I successfully created the shape I wanted, but because this will be duplicated many times over, it is too high poly for my PC to handle. Is there are more efficient way to make a tank track like this?
Here are couple of ways you can optimize performance:
Instead of making duplicates of track pieces try to Duplicate Linked. Use Alt + D combination instead of Shift + D. When you use Duplicate Linked you are not making copies of mesh. Instead, you are using the same mesh in many objects. That should save you some RAM.
In Subdivion surface modifier of a Track object reduce number of Levels Viewport to 0. In that way you are not gonna show subdivision modifier in the viewport, only on render.
Probably in the viewport you don't need to render all the track objects. Try turning it off by toggling this button: To activate this button you need to go to the Filter menu:
After all these tweaks try make a test render of your scene. Cause I suppose even if your scene shows fine in viewport doesn't mean you'll be able to render it (cause it does a different kind of calculations).
If after all these are done your computer still can not handle that much of geometry then probably you need to create low poly version of a track. When 2 subdivision levels applied to a piece of track it has 109,632 triangles, that's way to high. Even if we disable sub-d it has 6,852 tris. Taking into account that you need possibly a hundred of those pieces that is quite high.
Could you please share your solution? I'm really curious. I'm learning 3D and yesterday I saw your post and tried to model myself the piece you had problems with and I also found it very tricky. Here is what I come up with:
The steps I've done:
Make base shape with Subdivision surface (level 3; maybe level 2 is good enough though).
Apply Subdivision surface modifier to have denser topology.
Then add a plane and create shape that we gonna you to make a cut. Like this:
4. Make an Intersect (Knife) cut. We gonna receive this: 5. Mirror: 6. Clean up topology a bit: 7. Delete faces below the edge: 8. Add missing geometry: 9. Add control loops around edge (using Bevel Ctrl + B): 10. Add Subdivision and Solidify modifiers:
It is a bit messy and requires a further cleanup but probably a good starting point.
What do you think about this solution? Maybe you found a better one? I would appreciate it if you share. For those who might be interested I was trying to model this part:
I have read other solutions with cylinders in this thread and generally recommend to generate more geometry, the problem is that in this case I think that both cylinders would have to double maybe triple edges to have the support loop that is required to eliminate that pinching, and I think that would make me quite difficult to model the rest of the object.
Update: I successfully created the shape I wanted, but because this will be duplicated many times over, it is too high poly for my PC to handle. Is there are more efficient way to make a tank track like this?
Here are couple of ways you can optimize performance:
Instead of making duplicates of track pieces try to Duplicate Linked. Use Alt + D combination instead of Shift + D. When you use Duplicate Linked you are not making copies of mesh. Instead, you are using the same mesh in many objects. That should save you some RAM.
In Subdivion surface modifier of a Track object reduce number of Levels Viewport to 0. In that way you are not gonna show subdivision modifier in the viewport, only on render.
Probably in the viewport you don't need to render all the track objects. Try turning it off by toggling this button: To activate this button you need to go to the Filter menu:
After all these tweaks try make a test render of your scene. Cause I suppose even if your scene shows fine in viewport doesn't mean you'll be able to render it (cause it does a different kind of calculations).
If after all these are done your computer still can not handle that much of geometry then probably you need to create low poly version of a track. When 2 subdivision levels applied to a piece of track it has 109,632 triangles, that's way to high. Even if we disable sub-d it has 6,852 tris. Taking into account that you need possibly a hundred of those pieces that is quite high.
@PolyDoge Looks like there should be more than enough geometry in the existing model to get a passable result.
The key is to use the existing geometry as support by offsetting the edges in the intersecting shapes so there's room for the subdivision smoothing to average things out. It's also important to preserve the accuracy of the geometry in the intersecting shapes. Deforming large sections of the geometry can potentially create it's own set of issues which tends to increase the visibility of some minor smoothing artifacts. It's generally better to use the space between the edges of the intersecting shapes as a place to offset any differences in the underlying geometry.
A few posts back there's an in-depth write up that covers the basics of this process on cylinder to cylinder through hole shapes. The same basic principles apply here only the intersecting cylinder geometry projects outwards instead of inwards. https://polycount.com/discussion/comment/2757662/#Comment_2757662
Arbitrarily increasing the density of the starting geometry does tend to improve the accuracy of the basic shapes and that should make it easier to minimize [hide] certain types of smoothing artifacts but it's a brute force method that doesn't always address the underling issues that are causing the smoothing artifacts.
Once the amount of geometry in a mesh passes a certain point it just makes things harder to work with. So there's a threshold for just how much geometry makes sense for a given project and often the bar is much lower than expected. Maintaining the consistency of the geometry can go a long way towards reducing the amount of geometry required to accurately hold the shapes. Here's a link to another write up that looks at the relationship between geometry consistency and mesh density. https://polycount.com/discussion/comment/2746328/#Comment_2746328
Using the existing edges in a mesh to create new shapes makes sense for poly modeling but with subdivision modeling it often creates topology that requires additional support loops to hold the shapes when the subdivision smoothing is applied. While this generally doesn't cause a problem on flat surfaces, these additional support loops do tend to disrupt the consistency of the segment spacing on curved surfaces. Which tends create inconsistencies in the smoothing that will generate visible artifacts.
Placing these additional support loops can also deform the shape of the geometry which will also tend to produce smoothing artifacts. A couple of posts back there's also another write up that covers how support loop placement affects smoothing artifacts. https://polycount.com/discussion/comment/2757752/#Comment_2757752
Matching the segments of the intersecting shapes, whenever it's reasonable to do so, is also helpful for maintaining the shape accuracy of the starting geometry and will make it easier to place support loops. So it's generally considered best practice to start the modeling process by blocking out the shapes and figuring out the topology flow at the lowest possible level of complexity before adding all the rest of the support geometry.
There's a lot of different ways to approach modeling this shape but the same basic principles of matching the segments, offsetting the edges of shape intersections and maintaining the consistency of the geometry all apply.
Here's an example of what this process could look like when the shape block out and segment matching is done in a single step.
Start by creating the basic shapes and adjusting the number of segments in both cylinders so there's roughly equal spacing and the shoulder on the larger cylinder lands between a segment on the smaller cylinder. Run a boolean union operation. Bevel / chamfer the edges of the shape to create the basic support loops.
Split the shape in half and apply a mirror modifier. Clean up any stray geometry using merge by distance, snap vertex merge and limited edge dissolve. Cut in additional edge loops to connect the remaining edge segments on the intersecting shape. Use limited dissolve to remove any remaining edges that could cause smoothing issues.
Mesh cleanup could be done immediacy after the boolean operation with merge by distance and snap vertex merge. Using this order of operations would be much faster since there's less cleanup after the bevel but the trade off is it would deform the geometry before the support loops are in place to take up the slight differences between the shapes. Whether or not this is acceptable comes down to how accurate the shapes need to be, based on how closely they will be viewed by the players.
An additional support loop can be placed around the base of the smaller cylinder if a sharper transition between the shapes is required. This will also resolve the surrounding area to quads but may produce a very minor smoothing artifact that's only visible at extreme glancing angles. Given the size of the mesh and the player's point of view, relative to that part of the mesh, this would likely be a non-issue.
The same basic strategy and order of operations will work on denser meshes that can support tighter edge loops and will tend to have a slightly higher level of shape accuracy. Whether the additional complexity of a denser mesh is worth it will depend entirely on the results and the goals for the project.
Recap:
There will be situations where it's necessary to increase the
segment count on a curved surface to resolve some minor smoothing
artifacts but it's usually possible produce acceptable results without
having to double or triple the amount of starting geometry. So it's
important to fully utilize the existing geometry as support by
offsetting the edges of shape intersections and matching the segments of
intersecting shapes wherever possible.
and I wanted to ask about the optimization of the geometry itself, because I will be rigging the tank
Hm... Are we still talking about the tank tracks? Cause I don't understand what relation track geometry optimization has to rigging.
Here I created two low poly versions on track using boolean workflow:
Geomtery:
The version with bevels has some small issues with shading, but they are not gonna be noticeable unless you zoom quite close.
It all depends on how close you gonna show tracks on render. If not really close then maybe geometry can be simplified even more. If you want to show tracks pretty close, then maybe you want to use the version of track with Subdivision surface modifier for those pieces that are close and low poly version for pieces that are further from the camera.
You can check out the low poly versions I created in the attachment.
Im a bit struggle with this. What would be a better solution for "problem" area? After subD it, obviuosly, gives a bit ugly shading. Im not sure which options would be better - try to changing top cylinder sides to lover value. Or find some way to reroute edges on problematic area?
Im a bit struggle with this. What would be a better solution for "problem" area? After subD it, obviuosly, gives a bit ugly shading. Im not sure which options would be better - try to changing top cylinder sides to lover value. Or find some way to reroute edges on problematic area?
Hi. Looks like you have a shading issue because you moved one vertex that forms the shape of a cone.
Here is a bit more detailed explanation:
Here is how I would do it: As you can see I used a cutter with more segments. In that way I have a more consistent topology. Avoid moving vertices marked with green along these edges marked with blue: Cause that will disrupt the shape of the cone.
Looks like you have a shading issue because you moved one vertex that forms the shape of a coneAs you can see I used a cutter with more segments. In that way I have a more consistent topology.
Thanks! Yup, cutter defenitely should just have more edges, basically it was the major problem. I complitely overthinking it and try to figured out some other solution rather that just use more segments
There will be situations where it's necessary to increase the
segment count on a curved surface to resolve some minor smoothing
artifacts but it's usually possible produce acceptable results without
having to double or triple the amount of starting geometry. So it's
important to fully utilize the existing geometry as support by
offsetting the edges of shape intersections and matching the segments of
intersecting shapes wherever possible.
You're absolutely right, thanks man, very clean explanation
Thanks for the help @Cake_Seller. Yes, if I crank up the bevel modifier and subdivision surface modifier the issue becomes pretty much unnoticeable, but I am still concerned I that I have sub-optimal topology and am just covering it up with lots of extra geometry from the modifiers. Is there a better way to make the this object such that it looks good even without having to hide behind cranked up modifiers?
I am still concerned I that I have sub-optimal topology and am just covering it up with lots of extra geometry from the modifiers.
I see many people recommend, well, "don't fix it if it's not broken". Does your topology make shading artifacts or do you know that it will definitely cause issues later? Does extra geometry affect performance? If not then maybe there is no reason to fix it yet. Unless of course, you use it to practice in making good topology. If this is the case then I would recommend you to not use the Bevel modifier and try to add all support loops manually.
Replies
Is there a better way to make a 180 degree pipe intersection? My attempt was just merging the two mesh together in boolean, but the intersection topology isn't good as well as the sharp corners.
One way to tackle this is to model it flat and straight, then bend it into the shape you want.
Note that I didn't take the skewed part of it into consideration, nor the details at the top. I'm only trying to show you how to get the details in without messing with the curve. The important thing is that the curve needs a consistent amount and spacing of edges, or it will end up wonky like your result.
I want the wall thickness at 1mm and edgeloops at 1mm, so I start with a plane that's 38mm long, and with (Length-1=37) lines going through it. That leaves me with 1mm strips.
-----
If you want the entire thing to have a skewed thickness like your ref, this is the time to add it in. I didn't add it in and it won't be shown. For 3ds max, a soft ramp FFD is all that's needed.
-----
Then I plan to have a 1mm "ceiling" and "floor", so I add those in.
Then I want the internal strips to end 2mm above the floor, so I add that in, and their supporting edgeloops.
The point is to get this selection of polygons ready. This is the surrounding structure and the ribs within, all with 1mm edgeloops ready to go.
I shell that plane by 1mm to generate a back wall, then extrude those polygons by however much I want.
Two symmetry modifiers later and I have my final shape
One bend modifier later and I have the final shape.
Turbosmoothed isoline
Closeup
You can adjust what part of mesh will bend using SimpleDeform modifier's Limits properties:
I use an Empty object as the origin for SimpleDeform modifier to adjust how exactly mesh should bend.
To make slopes you can use the Lattice modifier. Assign a vertex group to specific vertices that you want to deform. Also set Interpolation: Linear in Lattice object's properties.
Of course, when you want to add more details, you might have to apply modifiers. It's not always possible to continue keeping it non-destructive.
If you increase the number of segments in your ring twice the crease will be much less visible:
I know there are real gurus on this forum, so probably someone will give better advice.
After I press R to rotate the lattice vertices, I press Z to rotate only along the Z-axis. Unfortunately, the ScreenCast Keys addon does not register those keystrokes.
-Apply the lattices that makes the end thinner and the one that bends the end
-Choose a face that is rotated at a good angle before the rotations start falling apart
-Add a transform orientation for the face on the top middle
-Select an edge on the bottom loop if you have more loops
-Make a face from that (lock the axis to X or Y when editing so the face`s orientation is consistent to that of the edge, which is where the transform orientation comes in handy)
-Select the verts that come after that edge
-Turn on snapping for face, set to active, and turn on project individual elements
-Set the transform orientation to global
-Go in orthographic top view
-Snap the verts to the face on the Z vertical axis (Z in Blender and Y in other software)
-Repeat the same steps for each loop
-Done
The first picture is the lowest LOD and the second one is me trying to figure it out but its getting really messy and starting to lose the curve. The blue piece is one of the original Booleans. I work in Maya, All and any advice is appreciated!
I'm trying to make the hinge on my model of these tank tracks. I followed a 3DS Max tutorial and tried doing it in Blender. the results were not good. Is there a better way to do this in Blender?
- Instead of making duplicates of track pieces try to Duplicate Linked. Use Alt + D combination instead of Shift + D. When you use Duplicate Linked you are not making copies of mesh. Instead, you are using the same mesh in many objects. That should save you some RAM.
- In Subdivion surface modifier of a Track object reduce number of Levels Viewport to 0. In that way you are not gonna show subdivision modifier in the viewport, only on render.
- Probably in the viewport you don't need to render all the track objects. Try turning it off by toggling this button:


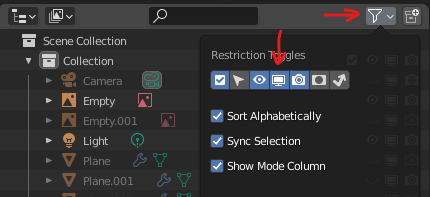
- After all these tweaks try make a test render of your scene. Cause I suppose even if your scene shows fine in viewport doesn't mean you'll be able to render it (cause it does a different kind of calculations).
- If after all these are done your computer still can not handle that much of geometry then probably you need to create low poly version of a track. When 2 subdivision levels applied to a piece of track it has 109,632 triangles, that's way to high. Even if we disable sub-d it has 6,852 tris. Taking into account that you need possibly a hundred of those pieces that is quite high.
What CPU/GPU, how many RAM are you using?To activate this button you need to go to the Filter menu:
Here is what I come up with:
The steps I've done:
4. Make an Intersect (Knife) cut. We gonna receive this:
5. Mirror:
6. Clean up topology a bit:
7. Delete faces below the edge:
8. Add missing geometry:
9. Add control loops around edge (using Bevel Ctrl + B):
10. Add Subdivision and Solidify modifiers:
It is a bit messy and requires a further cleanup but probably a good starting point.
What do you think about this solution? Maybe you found a better one? I would appreciate it if you share.
For those who might be interested I was trying to model this part:
I have read other solutions with cylinders in this thread and generally recommend to generate more geometry, the problem is that in this case I think that both cylinders would have to double maybe triple edges to have the support loop that is required to eliminate that pinching, and I think that would make me quite difficult to model the rest of the object.
Hm... Are we still talking about the tank tracks? Cause I don't understand what relation track geometry optimization has to rigging.
Here I created two low poly versions on track using boolean workflow:
Geomtery:
The version with bevels has some small issues with shading, but they are not gonna be noticeable unless you zoom quite close.
It all depends on how close you gonna show tracks on render. If not really close then maybe geometry can be simplified even more. If you want to show tracks pretty close, then maybe you want to use the version of track with Subdivision surface modifier for those pieces that are close and low poly version for pieces that are further from the camera.
You can check out the low poly versions I created in the attachment.
Im a bit struggle with this. What would be a better solution for "problem" area? After subD it, obviuosly, gives a bit ugly shading.
Im not sure which options would be better - try to changing top cylinder sides to lover value. Or find some way to reroute edges on problematic area?
Here is a bit more detailed explanation:
Here is how I would do it:
As you can see I used a cutter with more segments. In that way I have a more consistent topology.
Avoid moving vertices marked with green along these edges marked with blue:
Cause that will disrupt the shape of the cone.
Here is the result I get with subdivision level 2 and 2 segments of the bevel:
Is this result good enough?
Here is the mesh:
Also I used 24 segment cylinders instead of 20 segments, but I don't think it will make much of a difference.
What level of subdivision and number of Bevel segments do you want to have? Level 1 and 1 segment?