Hi guys
I have a big question for you today.
I was trying to better understand the 3 edge-loops technique for hard surface modelling in 3ds Max when I discovered this kind of corner that in my little experience is not possible to subdivide without having noises on the surface unless another technique is used (nurbs modelling or creasing by smoothing-groups).
I can't really find a way of sorting it out and there isn't any specific tutorial on internet, I hope someone can give me the solution.
In this kind of shape the 90° angles subdivides correctly with the 3 edge-loops technique, the 270° angle gives problems as shown in the pictures.
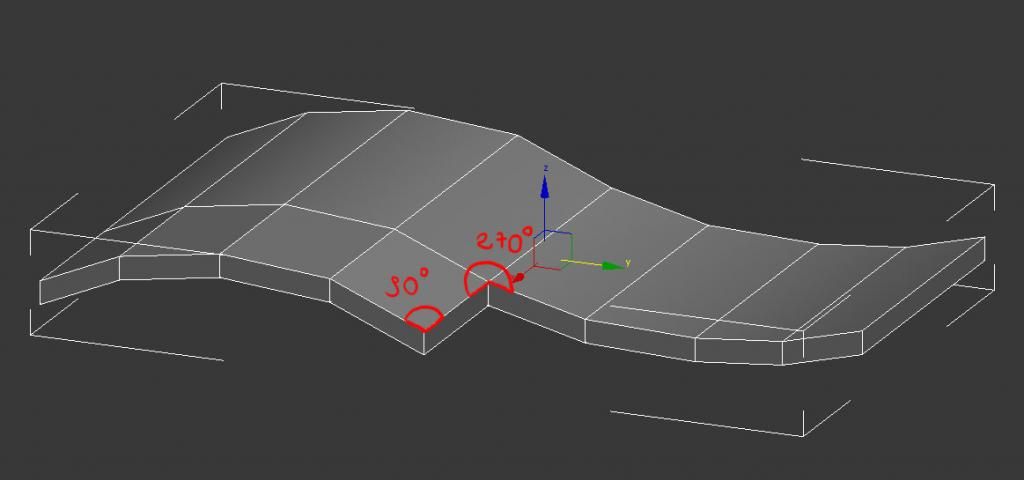
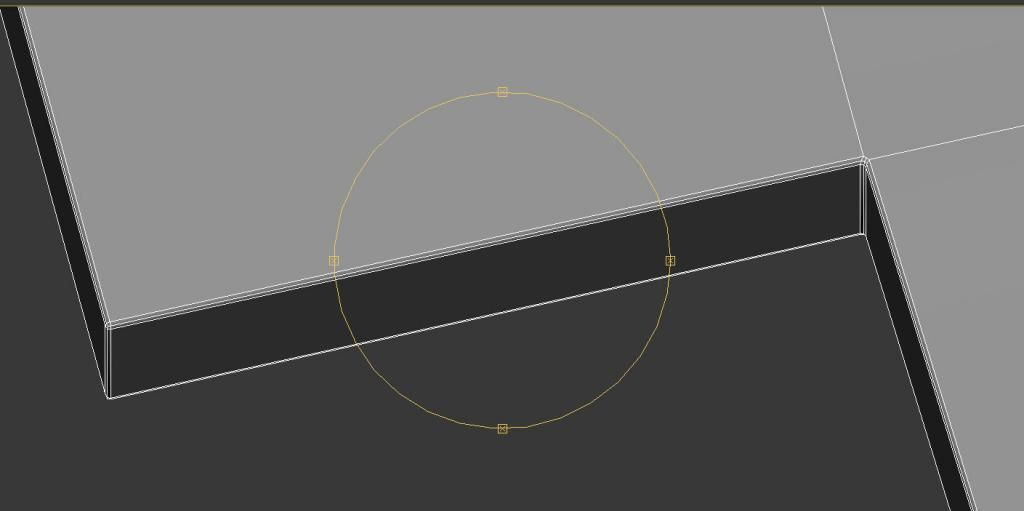
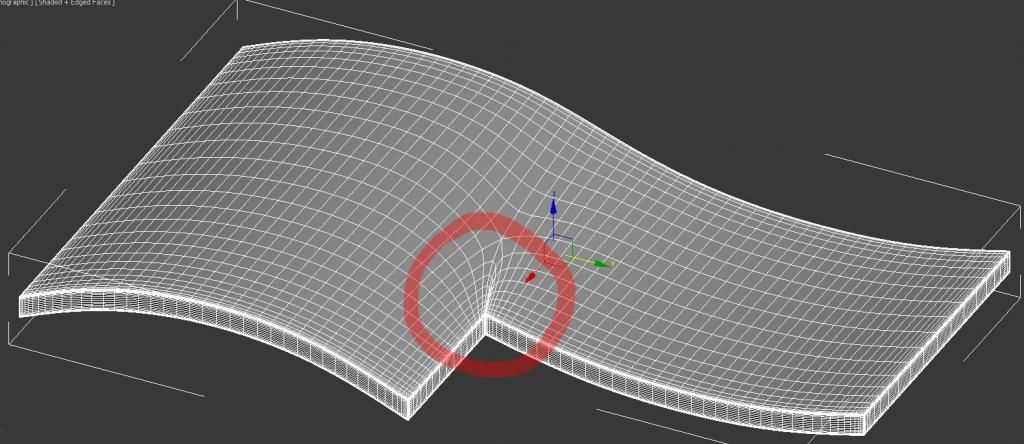
The fold created is huge and not acceptalble on a rounded surface.
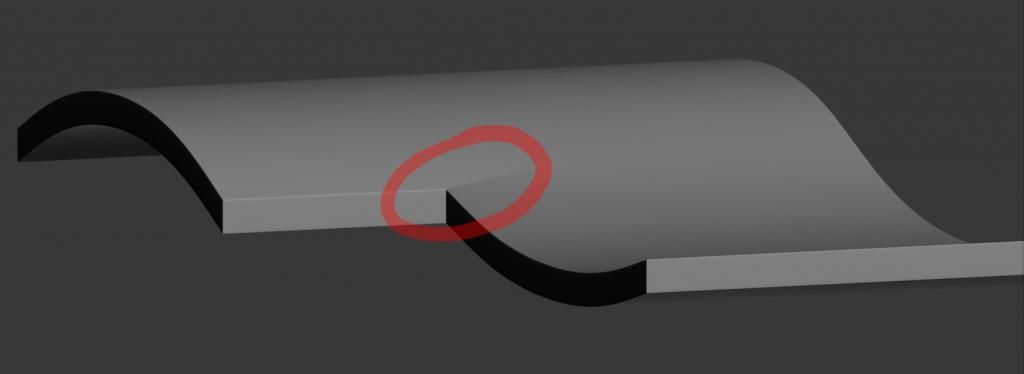
I've also tried to use Bevel tool in order to strengthen the creasing, but the result was even worst.
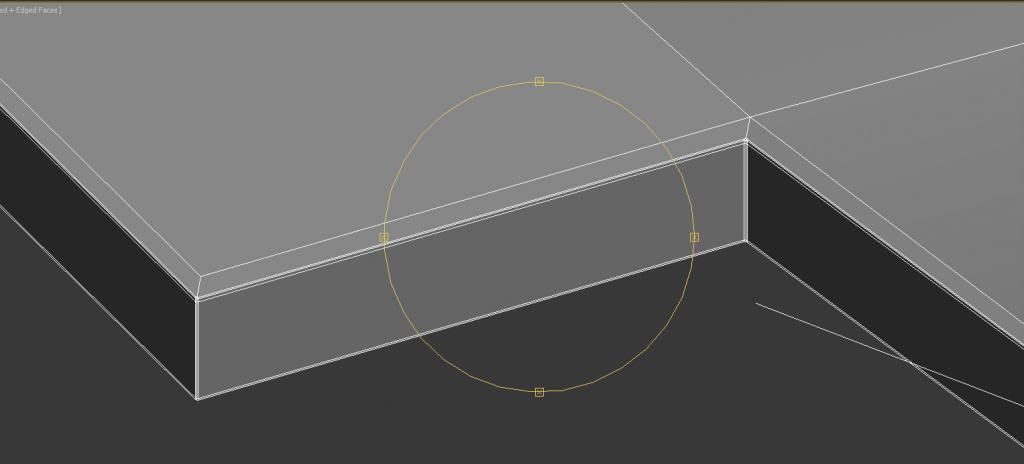
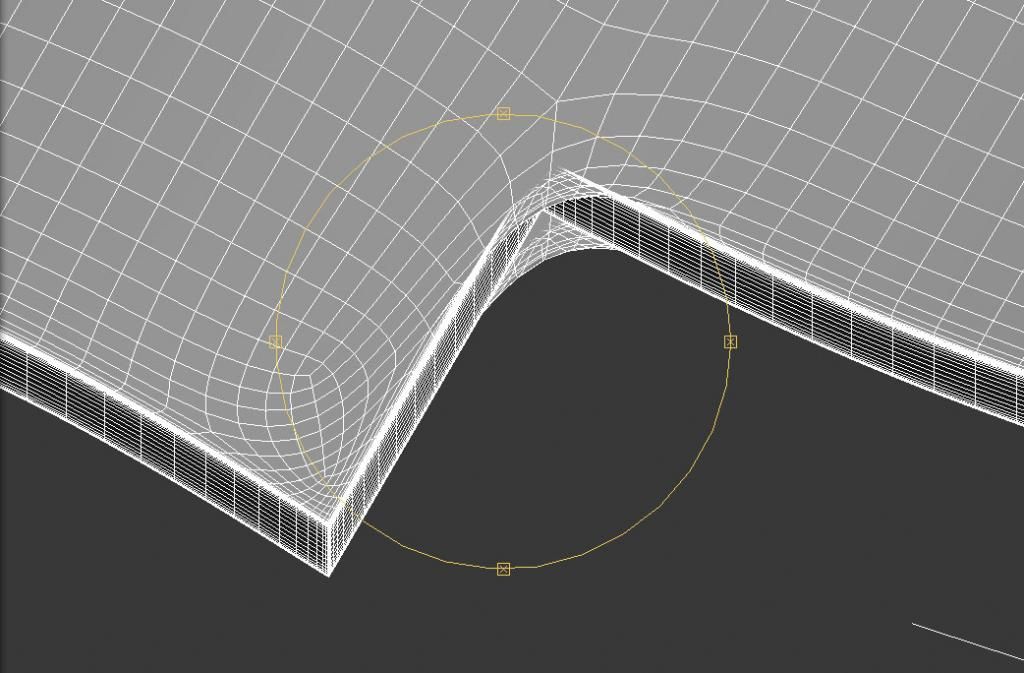
Any suggestion?
Thanks a lot in advance!
Replies
Dear Bartalon, thanks a lot for your reply.
I'm aware of that, maybe it is better if i use a more appropriate example.
This is almost the same case but with a spherical surface, here the extra loops would cause 2 hard lines on the spherical part.
How could it be sorted out?
The problem you seem to be having is that you're leaving the corner loop alone to fend for itself and not supporting it in some way.
This thread: http://www.polycount.com/forum/showthread.php?p=1393320#post1393320 has conquered this issue in quite a few posts so I would check it out when you get stuck.
Personally I would use a little more geometry to round out shape of the object which will give you some options to route that corner loop and it's supporting loops.
But there are probably different ways to handle it.
The last pic in Mark's last point kind of illustrates this- you can see the loops tight near the corner, but they eventually broaden out to help sell the outwards curve.
Yes My friend, it is true, but the subdivision by smoothing groups causes very sharp edges which is not always aesthetically correct, In my opinion the 3edgeloop technique is the most versatile and the one that allows you the best control on subdivision.
cheers :-)
Thanks for your precious opinion Rooster, at this point I wonder if Nurbs are not the best way of doing mechanical modelling. I mean maybe it would be better to make a retopoly of a Nurbs model and then crease it's edges than making a subdivision hard surface model from scratch.
What you guys think about ? How is your mechanical modelling workflow?