I've been posting a few images sporadically in the running "What are you working on" thread but there's no reason to flood that one with older images, and it might be helpful for anyone who has questions if there was a single thread.
I've been making toys for a number of years now. Some of them are based on the designs of fine artists, or video game assets, or graffiti artists, or graphic designers, etc.
Almost exclusively the toys have been produced from digital models. I use 3ds Max for building a base mesh, and Zbrush for adding detail, then going back to Max for retopologizing if need be.
Here's an example of a series of toys made from game assets. I was given a set of open non-watertight highly detailed Zbrush files for all three characters from God of War. These excellent sculpts were made by a group of artists for the video game, if anyone knows who made what, let me know.
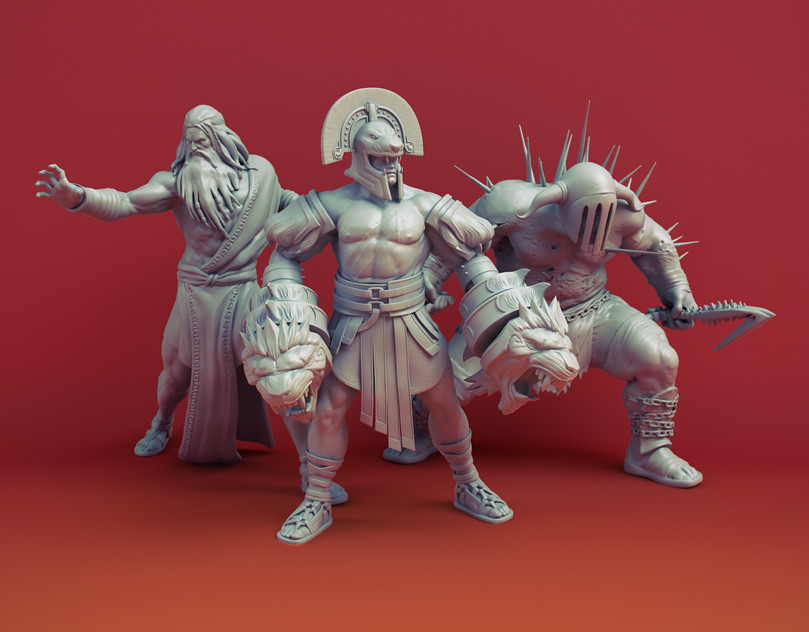
I had to rebuild all the meshes, using Topogun, and reproject the original detail on the the new watertight models. Then I resculpted, refined and added detail in Zbrush that didn't project well.
Then a seemingly never ending series of turnarounds got sent to the client for review, in order to tweak the poses just right. The models then get sliced up using boxes and booleans, in Max. At this point, the magic happens, and the models are printed using rapidprototyping.
Usually the output is cleaned, sanded, and prepped then recast in a very hard wax. The wax master is then engineered further with joints being added, or complex structures broken down into smaller, simpler parts.
Replies
Could you write up a short tutorial on how to get a digital sculpture ready for printing, and what's a good way to print it out (types of printers, materials, etc)?
That'd be really useful and interesting.
3D Printing is so expensive, I wouldn't want to throw that money away because I don't really know what to be careful of.
PS - the sculpts look awesome
Please post more! Those toys are great.
I own a rapid-prototyping company, and it's really cool to get to be part of the process. You never get over seeing digital art made tangible
Post more pics of the process, if you've got em!
There are two key issues to focus on when prepping a digital file for output, and a ton of little issues.
First and foremost, the model has to be watertight and "STL legal". A plane is not watertight, nor is a sphere that is missing even a single polygon. Everything in the model must have thickness. STL preparedness can easily be checked in 3ds Max, there is a modify in the drop down menu that will do the work for you. For a highpoly model it can take a very long time to process, but it will highlight holes, double polygons, etc.
Second, look out for thin parts that can support weight and tiny detail that will snap off the model. Everything must intersect for the output to be generated as a single piece. Thin legs or thin necks are bad. Hanging thin details like chains and ropes are bad. Bulk up the chains and have them intersect the main model. Again, easy to fix in Max, using the "Push" modifier.
Oh, and that image is NOT a photo.
Here are three images from the process:
First, the beautifully done high poly model from the developer. It's a terrific model and will work fine for projecting high poly detail onto low poly game art, or middle poly cinematic art. However, it can't be printed, since it is mainly open shells.
Second, retopologized with a watertight low poly mesh.
Third, projected high poly detail onto low poly mesh.
Fourth, fully detailed new high poly mesh from low poly mesh.
Sixth, cut up for printing.
Seventh, digital paint master for factory to reference and for marketing.
Urban vinyl collectible figure by Jamungo, designed by Clay Ferguson, who is a good friend and here in Austin. He gave me a very tight set of turnarounds that he had put together in Illustrator. Modeled in 3ds Max, mostly polys, a little bit of NURBs.
Produced and manufactured by 3Zero.
One of the final retail versions. Every few months, Jamungo releases a new design, with a full outfit, and sometimes new weapons:
Very interesting, I was curious how you did the chains for the guy on the right.
After it's cut for printing (Stage six), the pieces are made, are those individual pieces then connected back together before the wax mold stage?
Also, if the final toy is articulated, do you do that is is that stuff added further down the pipeline?
I was wondering, once you've recieved your print, do you need to do any sort of treatment on it like sandpapering out artifacts and/or any sort of touch up work at all?
If you would want to do some painting on your print, what would be a good paint/ink to use, or is it mostly airbrushing?
Does zbrush have a feature that checks your model for 3D print capability?(I dont use 3DS Max)
thanks again for an interesting read
-Martin
http://www.zbrushcentral.com/showthread.php?t=71266
3D Print Exporter for Zbrush
I haven't used this in a little while, but I believe it will tell you if you fail an STL check
Zbrush also has a "fill holes" function that will patch openings with a crude polygon. It breaks the subdivision levels but has some uses. I usually do all the patching and rebuilding by hand.
I didn't make the chains on that character, but I have made chains for other sculpts. Max is very very cool about chains. You can lay out a long chain and use a deform to path modifier that will move and deform the chain along a spline path. The spline path and the model both remain live so the path can be tweaked. It's good for ropes too.
The pieces are not rejoined before mold making, they are cut up in order to establish the early stage of articulation. The wax masters that are made from the output are modified by hand to incorporate final articulation techniques. So yes, articulation can be added further down the pipeline. It can also be done digitally, and some clients and projects require it.
Yes, the output requires quite a bit of refining. Even after the raw output is sanded and primed, a wax recast will sometimes be made in order to refine the model further.
It is possible to paint a well sanded and PRIMED output, but not recommended. It's better to make a silicone mold and recast your model in resin. This will give you a more physically stable model to paint, and you can make more than one to experiment with.
I modeled and engineered the original giant sized Bertie and all his weapons, back before the creation of 3A. I have a lot of material from that project, so let me see what I can dig up.
In the meantime here is a series of notes about the renders. Playdo hit me up in PM, I hope he doesn't mind, but he asked excellent questions that maybe, just maybe, other people would like to know.
The images of toys that I post are mostly renders. I do all of the development and design digitally, using Max and Zbrush, and it's very hard to take a great photo without a full blown studio set up with lights, backdrops and a good camera.
Although some of the models are produced as real, collectible artwork, I still prefer to show the renders. Some of the models have never been produced, so renders are all we have.
For the renders, I use Vray, which is available for a few different packages, although any good program will work, there is nothing all that special about the way I set up the scenes. They have mainly simple textures and simple lighting setup.
Sometimes I'll use a matte/shadow material on the background plane - usually when I need a plain white background, this results in no physical background in the render, just the color or image based virtual background. I never drop in a full blown background in PS, because there is too strong of a relationship between the lighting and reflection in the scene and the background. I do a lot of sweetening to the background in PS however, curves, hue/saturation, lens blur, diffraction effects, usually a hot spot, occasionally some dust or lightray effects.
No photometrics, just Vray lightplanes. No HDR for lighting or reflections, I used to, but fell out of the habit, and switched to lightplanes with gradient maps.
The plastic is a very very small noise in the bump, at a very low value somewhere from 2-5, usually 2 or 3. There are a couple of renders where I didn't drop the noise in bump, but rather in spec, but that's uncommon.
You know, we don't have a printer, we use a couple of great output services. We also have a few factories overseas that handle output, cleanup and reproduction for us, so we don't need to have an in-house device.
It would be great to have a rapid-prototyping machine in-house, to play with and print little toy tests on, but they are terribly expensive and require continuous upkeep. They also go out of date, and can later be replaced by newer better machines.
You didn't miss it, and that question brings up a great point that we always try to explain to customers. Digital sculpting can be printed at multiple sizes. You don't always need to have your scale set in your modeling software to the exact measurement for the final.
When modeling a 10 inch resin statue or a 8 inch vinyl figure, I'll rough out the model around that size. But at any point, the client might change the size of the final manufactured toy to 12 inches, or 6 inches. No problem.
However, when modeling something that is very engineering intensive, like a 12 inch articulated GI Joe style figure with a ton of joints, the precise measurements will be established up front, and we stick to them.
Example of a vinyl figure that could be printed at different sizes, MadBattleMan - designed by Mike Sutfin:
Big thanks for helping explain the practices and sort of pipelines that need to be dealt with. I'd love to produce some physical prints someday soon, as it always seems a shame to me that all of the work I do, never really leaves a monitor screen. The quirkiness of the designs in the "vinyl toy" scene is really appealing to me as well, compared to a lot of games/ films/ advertising.
Sam, I remember when you were looking into doing up some Ghoul School action. I know that I probably recommended that you have a nice broad audience first before investing the time and money. That's what we recommend for everyone. Know your audience, know your market. Otherwise you'll be very cramped at home with 100's of boxes lining your dining room. Anyway, you are a solid designer, someday you'll get something grab-able out there.
Churm is a slippery little guy, just looking for love.
I've actually been researching the topic as of late and couldn't find too much relevant information, and this thread is a God-send!
I do have a question. Earlier you answered to Sam with a suggestion to know your audience. But how exactly do you go about finding information about the audience and the specific part that you do? How did you guys break into it?
On one hand, there's an entire industry of marketing specialists who specialize in the specialty of finding out everything there is to know about a company's target market. On the the other hand, there are small independent creators who need to know how many people are interested in buying this or that piece of art.
There's no easy answer here. Pay attention to how many copies/units of something similar to your product have been moving in the marketplace. Pay attention to how many fans your Facebook page has, or how many comments your posts get. These are all examples of measurable metrics, but the difficult challenge is how to translate the numbers into strategy. What I mean is, you have 2000 fans, so how many copies of a toy do you make? 10 percent? Half a percent? I like half a percent as a good safe number.
Also, you don't have to be a pandering sell-out to be successful, but you do have to be aware as to what your market likes. This is also a massive challenge.
I just started working for sculpting toys and it is nice for me
to read your experience so far.
Thank you Wetterschneider
Like say on that first model, the body and the beard are separate objects in Max, but not on the final print. So does it know to just use the outer-most area? Or did you have to print the beard separately from the body?
Intersecting geometry is fine. You can have big old bodies and little decorative elements be individual and as long as they intersect with each other, the print will come our as a single piece.
Additionally, and more interestingly, SELF-intersecting elements work fine too. If the arms of your character are against the sides and part of the arm intersects the body... it will still print.
Errors are produced by polygons that are too small, floating elements that are unattached, open meshes that are not watertight, and single sided polygons.
So does it only print the outer shell? Or does it print one solid form for the whole thing? I mean, can you have the figure be hollow, or is it always solid?
To clarify, a 6 polygon cube with all polys facing out will be solid when printed.
A 6 polygon cube with all polys facing out that has a second smaller cube inside it with all polys facing in will be hollow when printed.
You should come out to the Polycount Austin meetup sometime!
We only have an online store where we sell directly, but a lot of stores around the world carry our product. We have a distributor out in Cali who handles our wholesale.
I'm not going to throw a direct link to the store here, since that's kind of bad form, I would guess - but you can get there through our big pro portfolio. The link is in my siggy.
i run a rapid prototyping company, we own a 3d printer and we also specialise in PU casting. here is a link to our website http://www.pdmodels.co.uk/
I would love the oportunitly to work with you guys. keep us in mind.
keep up the good work!
"Modern Hero" by Madl, and sculpted by me.
So you don't have to model the joints and breaks yourself then? That's cool, definitely something I'd be interested in getting into.
I do a fair bit of "pseudo-engineering" by cutting joints and articulating the figures, but a lot of it can be fine-tuned at the wax stage. For vinyl that is. It takes a special level of experience to make sure the soft vinyl can be pulled from the mold and assembled.
It's here, on Artstation:
https://www.artstation.com/artwork/kzB1K