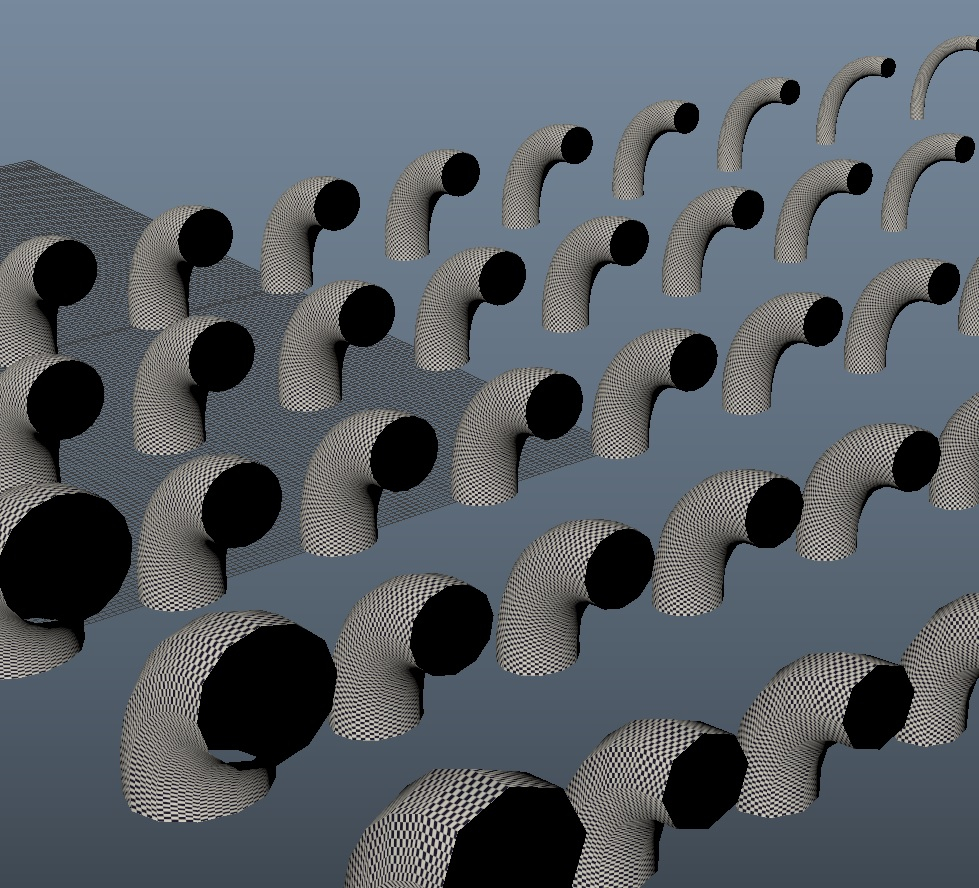
For my project, I am building a set of modular pipe pieces with different diameters. Currently all of the UVs are square-mapped from the 0-1 range so the pieces are perfectly tileable; however, depending on the thickness of the pipe, its UVs may be stretched too thin or too far on the V axis. I could scale the UV shell vertically, but then it would not be seamless when connected to other pipe pieces.
Would anyone care to share their insight as to what the best approach would be? I'm thinking of scaling the V axis by factors of 1 so that there would still be some distortion, but still be seamless. I'm not sure if there's a better method than this though.
There's also the matter of texel density, which I could address by making a few different texture sizes, but it still wouldn't be perfect. Do you think this would be a big deal?
Replies
This method is working pretty well I think.
there's quite a few ways to handle without doing anything complicated with your materials this but they'll depend on what the pipe actually needs to look like at the end.
if it's a pretty basic painted metal pipe with no seams - just bake the largest one down and map the others to it.
If texel density is a concern, do the same thing but on the smaller ones keep texel density correct and slice up the UVs so it doesn't look crap - thirding might work or if the diameter difference is too great then you'll want to be a bit more creative.
I just went on the wiki and searched for thirding.