This is the image
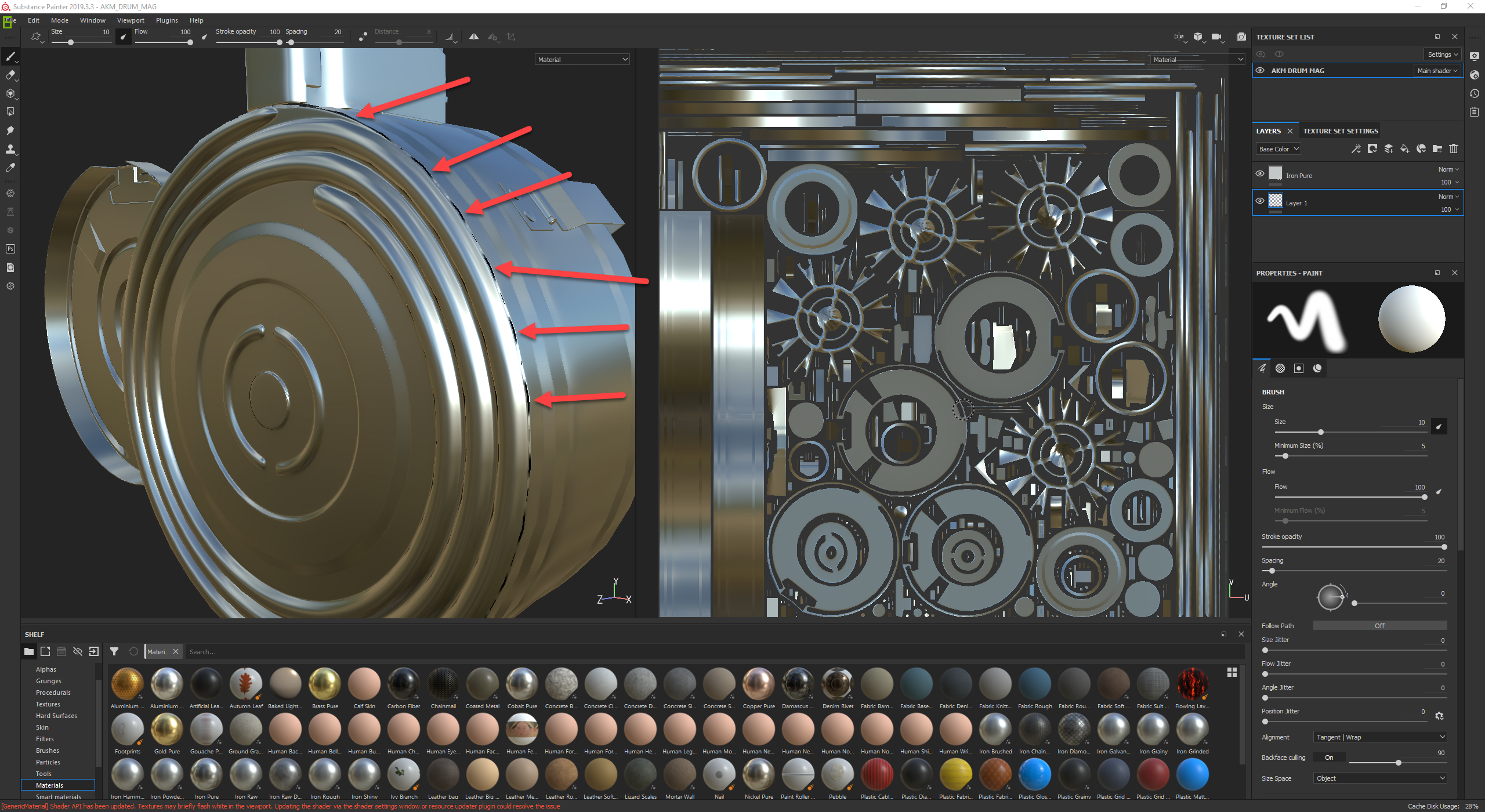
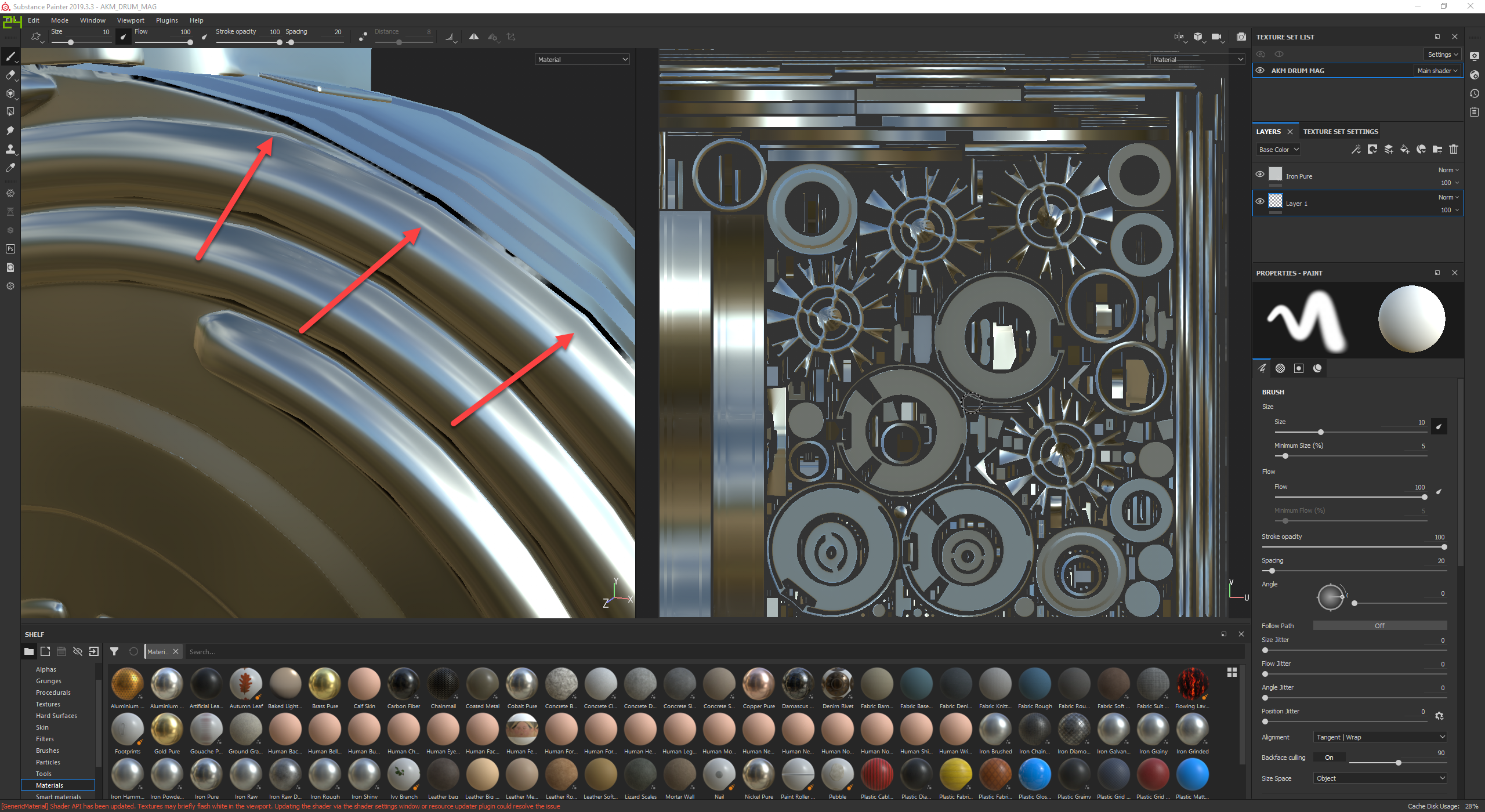
How can i fix these artifacts?
The pictures below show case why the artifacts are happening but i cant add more geometry or its not going to be usable in a game engine.
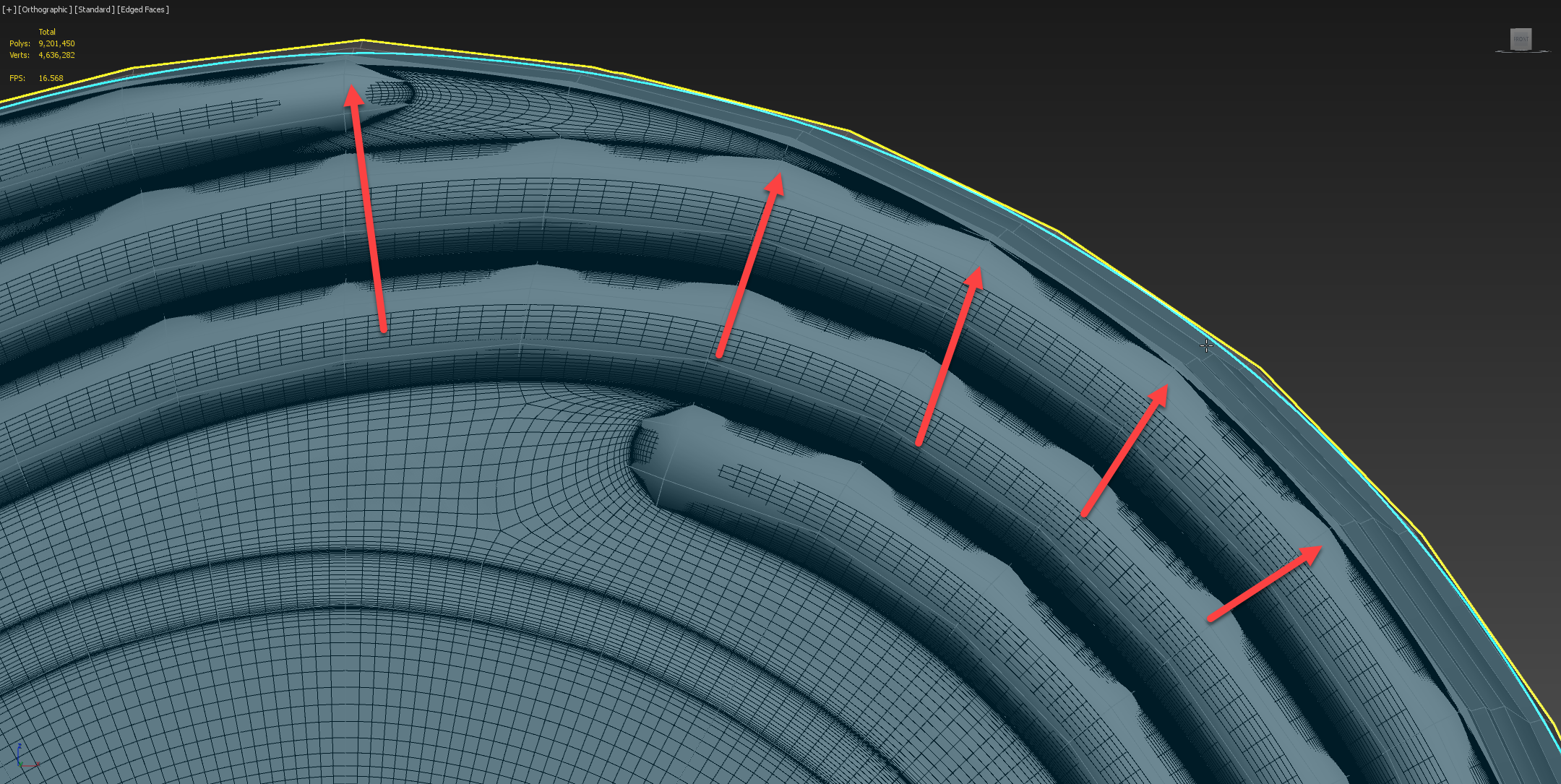
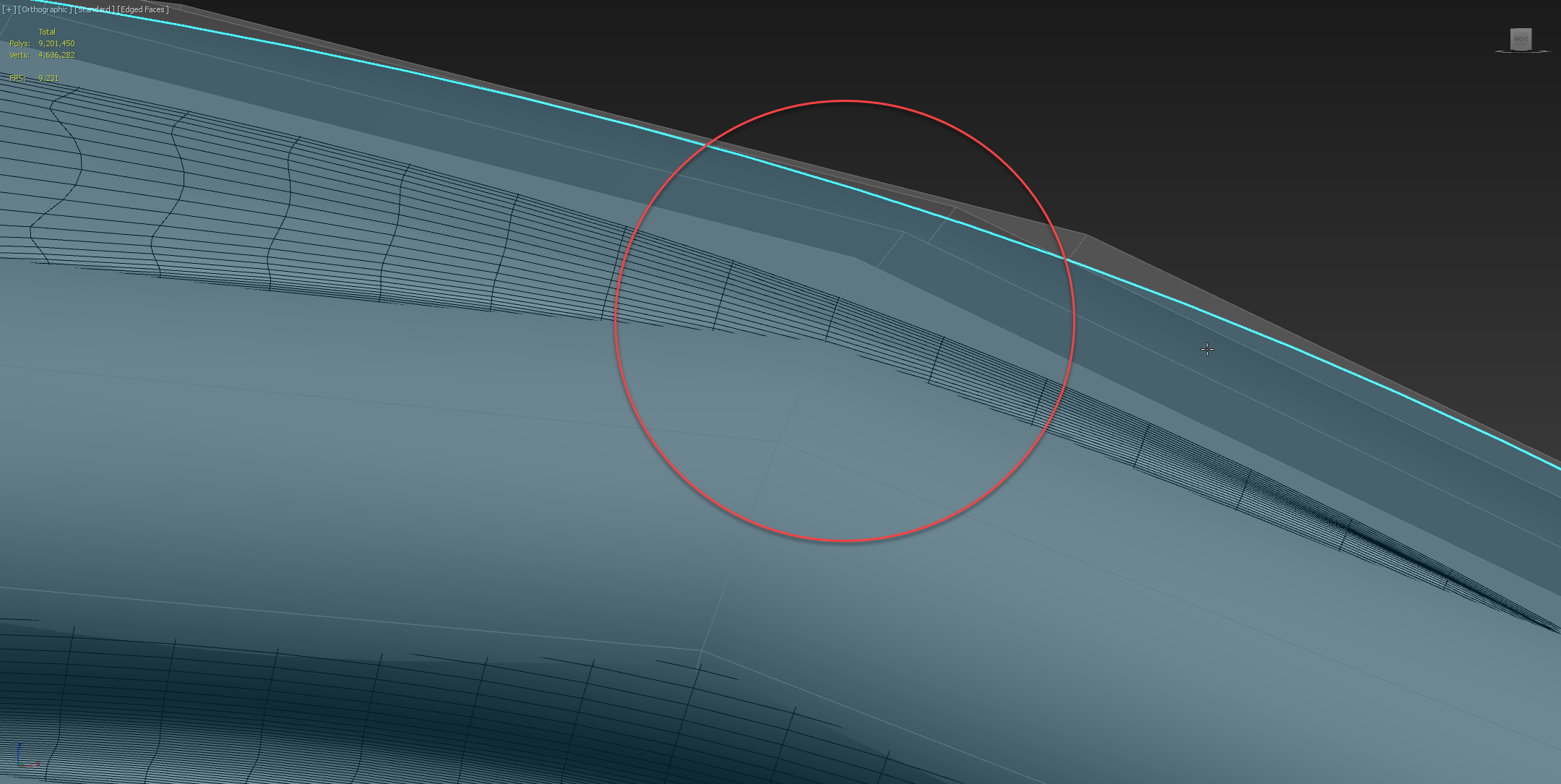
I tried adding edge loops inbetween each of the flat edges on the cylinder but the turbo smooth modifier shrinks the cylinder too much and causes these artifacts. What can i do to keep the same low poly model and still get a good bake without these black artifacts?
Also some of those spokes i know are completely screwed up in the UVs. I forgot to re copy the low poly i messed with over as highpoly and add the modifiers.
Let me know if you need anything to help figure it out.
Replies
There are always the same questions asked about the same poorly setup meshes.
When the basic technical understanding is missing and multiple issues are present is becomes hard without experience to see what is caused by what.