Hello, this is my first post here (dunno when this is gonna show up... heh.. anyway).
I figured I'd like to try taking my hand at this workshop while I'm trying to find some work. I haven't done much formal modeling so this thing is probably going to wind up fairly simple, but I like the concept.
Looking at bitmap's planned model inspired me to try coming up with some sort of Junkyard Tonfa. I was originally planning some sort of sword perhaps, but I can't seem to come up with something that could be considered a long blade but isn't 'already' a blade.
Components: C-Clamp, Kee Klamp internal joiner, Pipe fittings, Pipes, possibly more if i can solidify some ideas on hidden components for this weapon (I was thinking of some Rotary Hammer drill bits but I don't know if the size would be too small for this thing).
Modeling Progress (still looks fairly basic to me, I think it needs something more to make it pop a little more, like changing the coupling at the grip into a valve section... also missing the threading on the ends of the pipes and the clamp pin).
No BG
With BG
Concept of construction: the C-Clamp acts as the grip and the pin of the clamp acts as part of the method to hold the long end of the pipe section in place. The internal joiner acts as the simplest method of creating an attaching location for the end of the sections of pipe for both the short end and long end as it is already in two pieces and would need minimal welding work done to attach.
I'm trying to come up with some form of hidden weapon in which the long end of the pipe can be removed from its fitting to reveal a thinner bladed weapon of some sort attached via a reducer fitting on the inside. I'd considered possibly a pipe that has been split into two sections on the latter half, but it probably wouldn't be structurally sound. A chainsaw blade threaded into the pipe and around the outer section of the pipe might work, but again... structural integrity, but then again... the logistic of how it would hold still.
Yeah, I may have given this a little too much thought... Or maybe not enough... Maybe I'm just focusing too much on the logistical aspect of it. I'm still at the stage where I'm considering what high poly detail I can build I suppose. I haven't done much low poly work as of yet (just random projects I set myself on) so it'll be interesting when I have to figure out how to back the high poly down... haven't done that yet lol.
Considering I'm a fair bit of a beginner at this, don't worry about being brutal on this concept being kinda... erhm... silly? Gotta learn somehow.
References (sorry the internal joiner is so big, wasn't that size on the page):

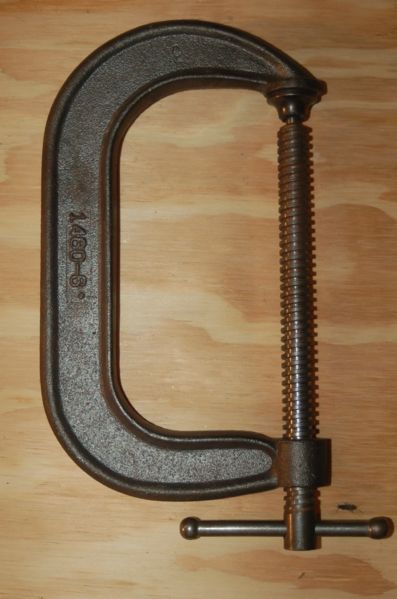


Replies
Its easy to come up with ideas its the implementing them where you can get stuck.
Good luck with it.
I'm about ready to cut off some slightly more detailed spots that make things harder to unwrap it, but I'm baffled as to why the UV's are completely unresponsive in some parts (rather, 70% of the model). Granted, I'm trying to model and UV this whole thing in blender but it strikes me as odd how the uv's react the way they are (probably would've been simpler to do in 3dsmax but I want to try to understand the workflow in a program I can afford to use professionally for the time being).
Bringing the model into 3ds max they all "look" ok (aside the part I didn't get to before realizing there was a blender UV problem). I'll have to look into their wiki or ask around blender boards for a solution if I find that the problem persists.
Anyway, this is where I'm at so far. I had to tweak some of my plans and am still debating a couple points on pieces I have modeled on (random bolts through the far end of the long side for extra damaging / possibly holding pipe together from a crack, considering making weld melt points or not, reworking of the UV arrangment). I had to hold back a week from working on it due to coming off of a vacation break and readjusting to some back breaking work.
Low Poly
High Poly
Checker Test on Low Poly
Obviously UVs still need some work. I think I need to model in that indentation into the C-clamp still (not sure if it's deep enough to need it). Bolts aren't modeled on yet. I didn't set up any smoothing groups when I brought the OBJ into max for a moment to check the UVs. Testing to import the obj into max then exporting it back out seems to get things working, so I might be able to salvage the work on it.
I actually could use some opinion on the setup of the model. I'm not sure if it is a good idea for this thing to be all one object, as I've got a few 12 sided cylinders blending into a few 6 sided ones, and it's making it difficult to make sense of the UVs. I can post an OBJ later if it would help. If I didn't try to keep this all one object I might be able to get away with opting for an 8 sided cylinder instead (I used the 12 sided for easier blending).