Hello Everyone! This is my first time using Polycount and posting, so be blunt with me. I can't improve if everyone tells me it's good as it is. Recently I have been into gun modeling and have been working on this project for about a 1.5 months on and off. I would say roughly 40-50 hours of work.
Link to project page.
This project's goal was to hone in on hard surface modeling in zbrush and further skills in substance painter for realistic texturing. I am satisfied with the end result and what I learned.
Things I could have improved and fixed:
- The fact that the Uvs are only on 1 tile really hinders the resolution of the texturing. I did go back and try to split it into 2 tiles but the baking process messed it up bad so I went ahead and stuck with 1 tile instead.
- I do not necessarily know what the "ideal" polycount is for weapons like this but I feel like 22k is a bit too much and I could have taken some time to further optimize the count.
- Some more texturing work could have been done to weather down the weapon more, especially the metal frame of the gun.
- Lighting and Rendering is not my strong suit so those are still improving constantly.
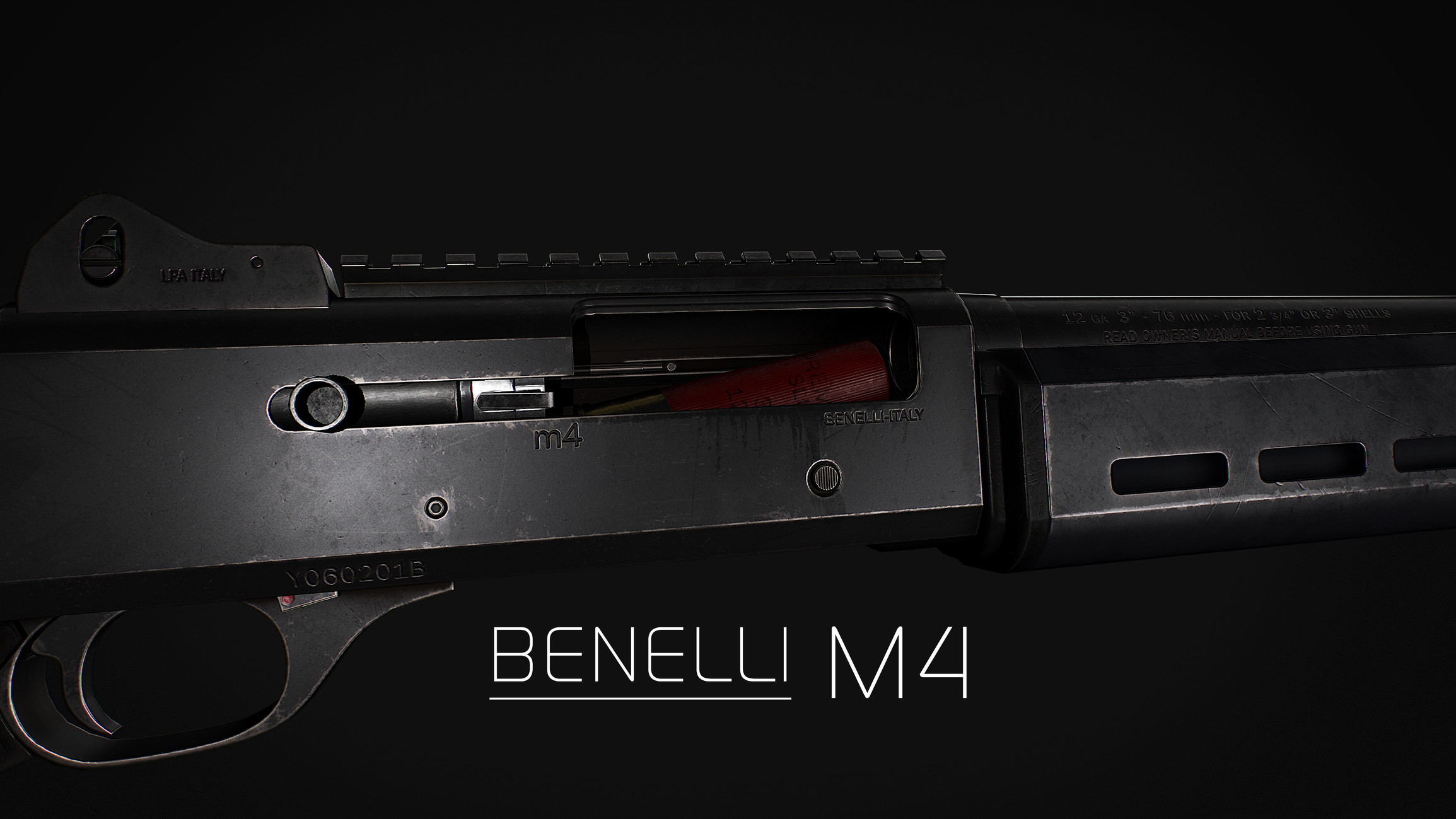
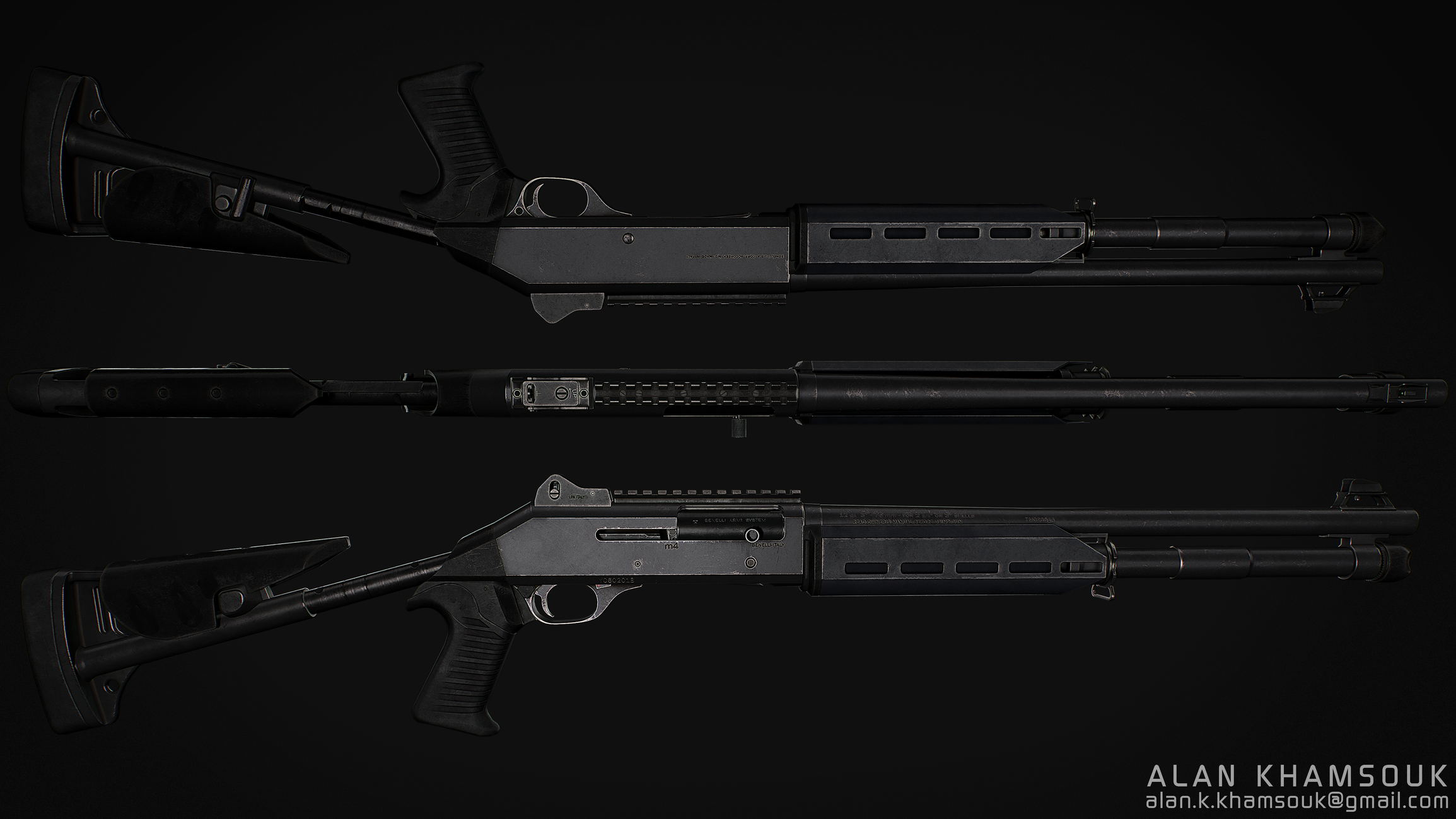
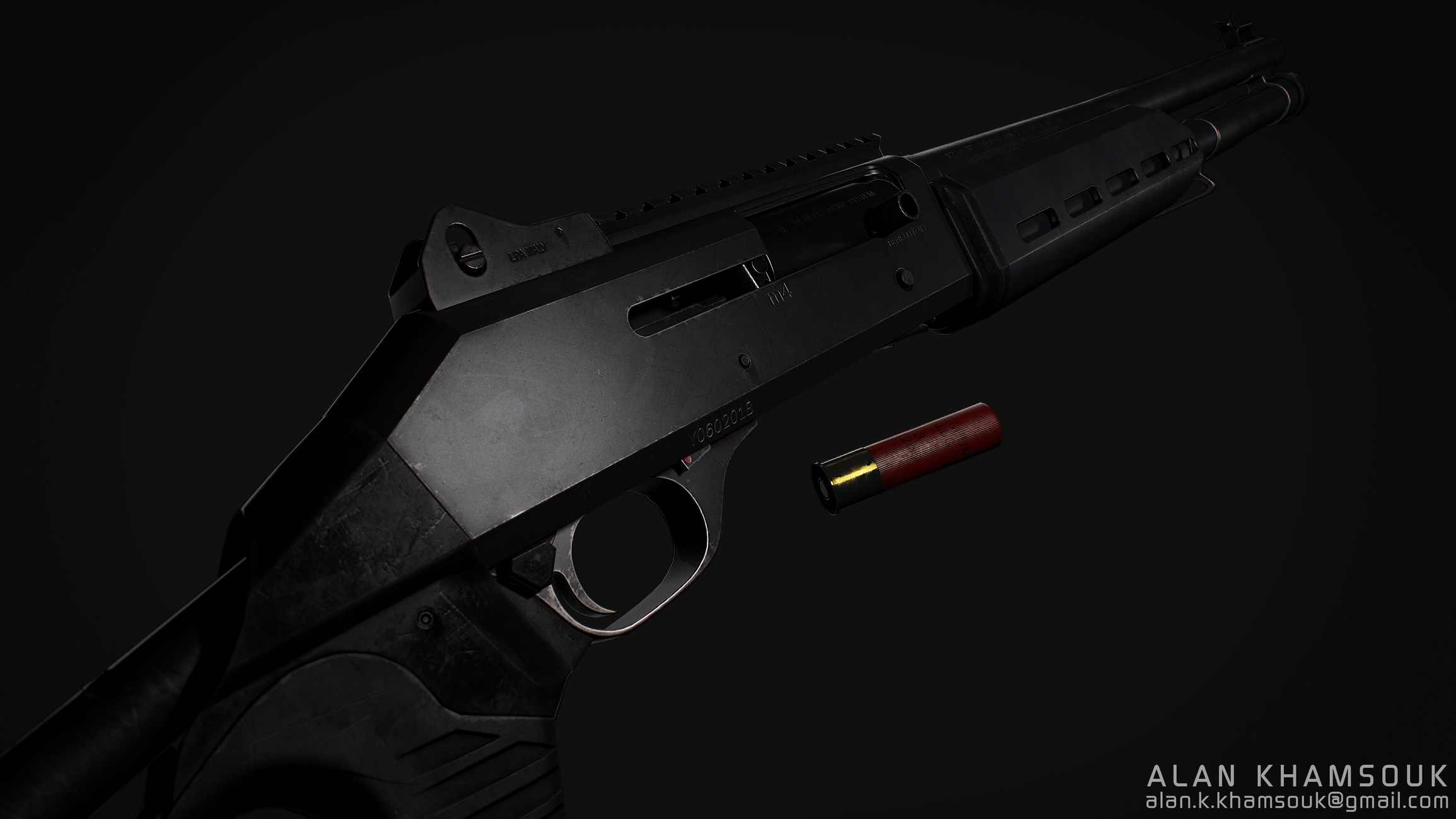
Replies
But there are a few things i would do different.
First, the metal body needs better definition, currently it doesnt read as metal, it looks more like pre-pbr metal. The most important channel is roughness and it looks like your roughness is almost the same everywhere with very little variation. Combining a good roughness variation with some metalness channel tweaks and you should get pretty close to what actual metal looks like. For example, the worn edges are bare metal so you should have a metalness value close to 1 and the roughness depends on what type of metal it is - probably aluminium - so you can google values for that.
I cannot stress enough how important scale is. If you get scale wrong in any of the features of your materials it will immediately stick out and break believability. The oil spill that happened under the ejection port makes me think of a wall with leakage, not vaseline being spewed out when the casing gets ejected. Another example would be the scratches witch are really big and looks like someone used this gun to stop a sword fight. Scratches should be subtle and not have continuity on surfaces that are not coplanar. Basically should end where there is a hard edge. Speaking of edges, they are a bit too sharp and dont read well at medium distance. Usually, i am not a fan of the extra smooth edges guide, but in this case i would say to soften them a bit because it doesnt look very realistic. Looks like you can cut yourself in the underbody of the gun.
Good luck!