I'm working with a modular workflow on my current project and am lost on how to handle corners.
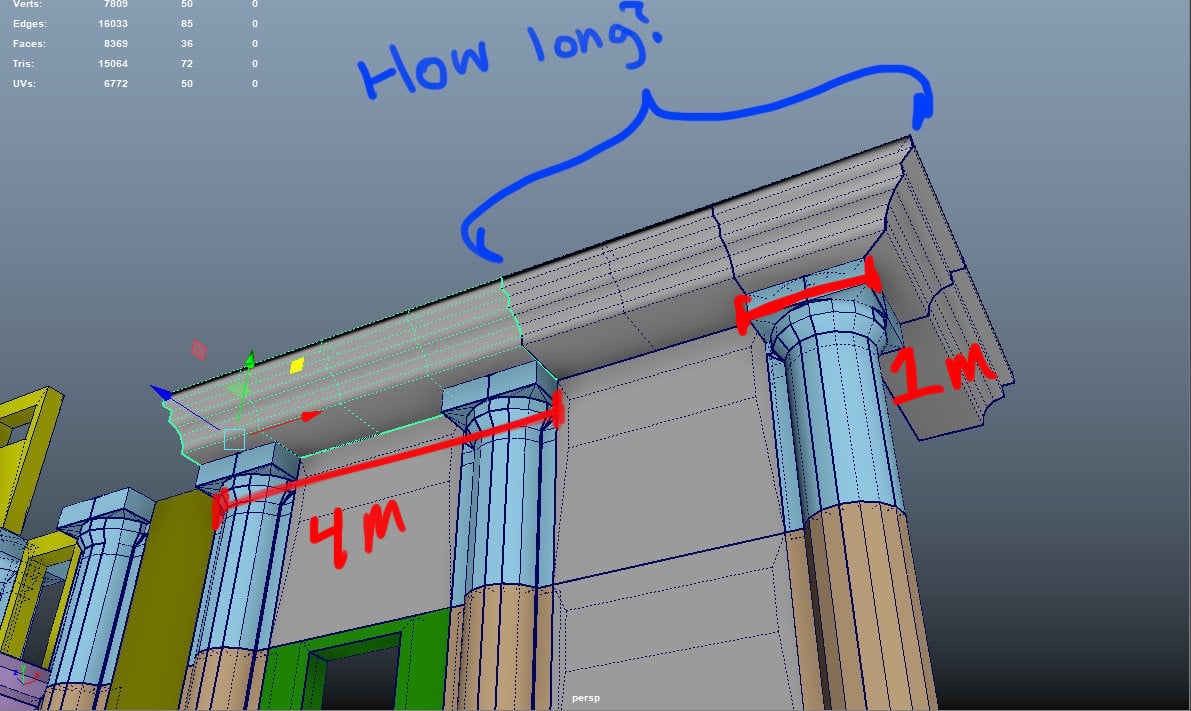
If my main trim is 4m meters long, its UVs look like this...
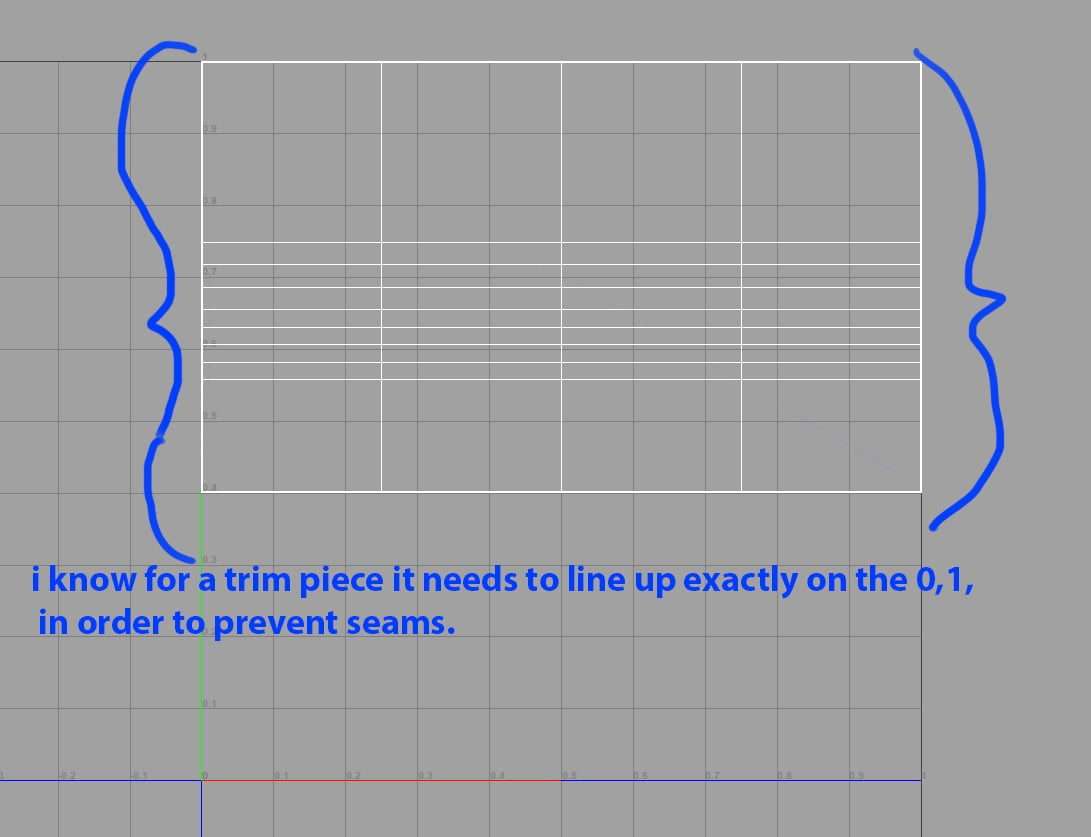
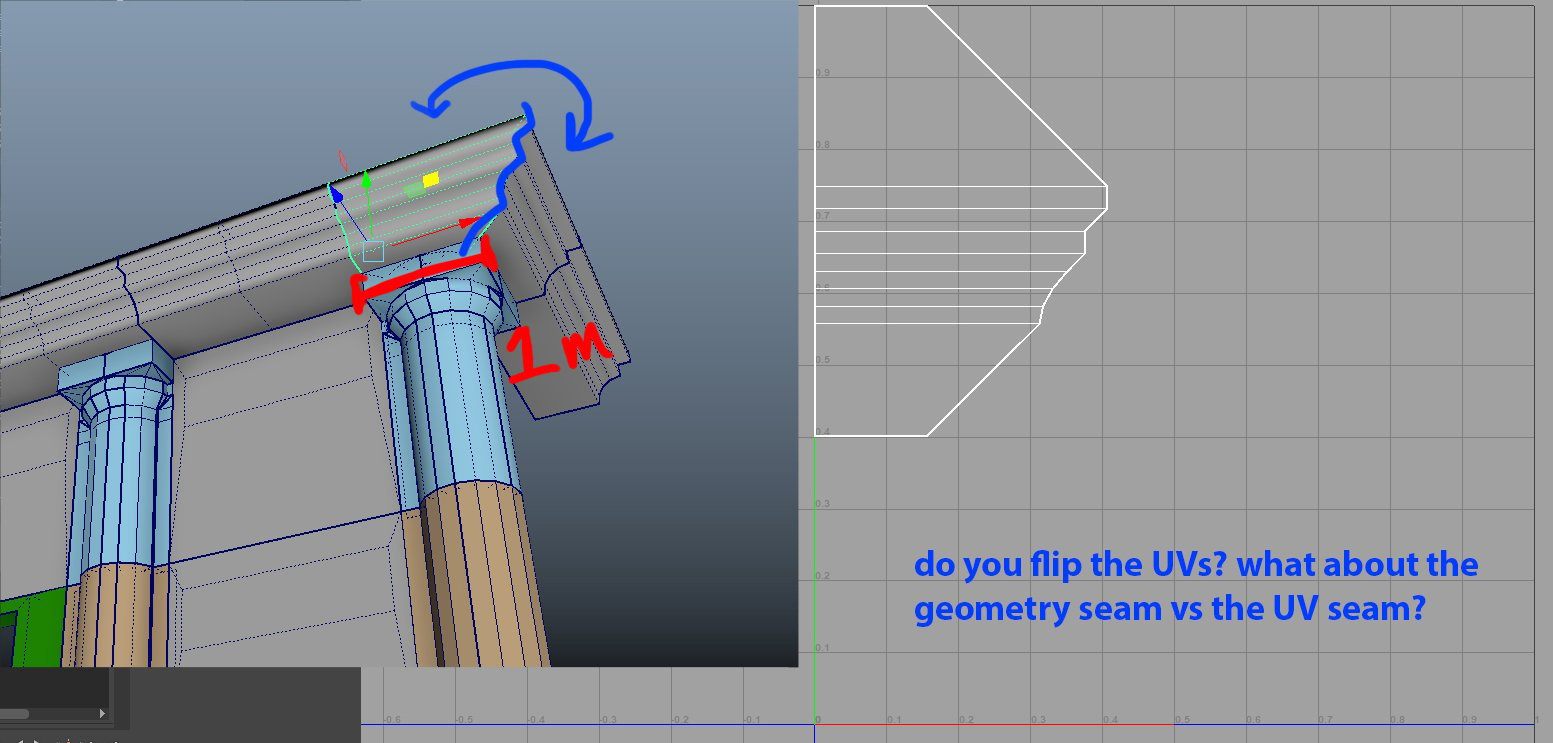
Despite not understanding how to tile the corners, I don't understand how to make other sizes of the trim pieces continue to be seamless without stretching the texture.
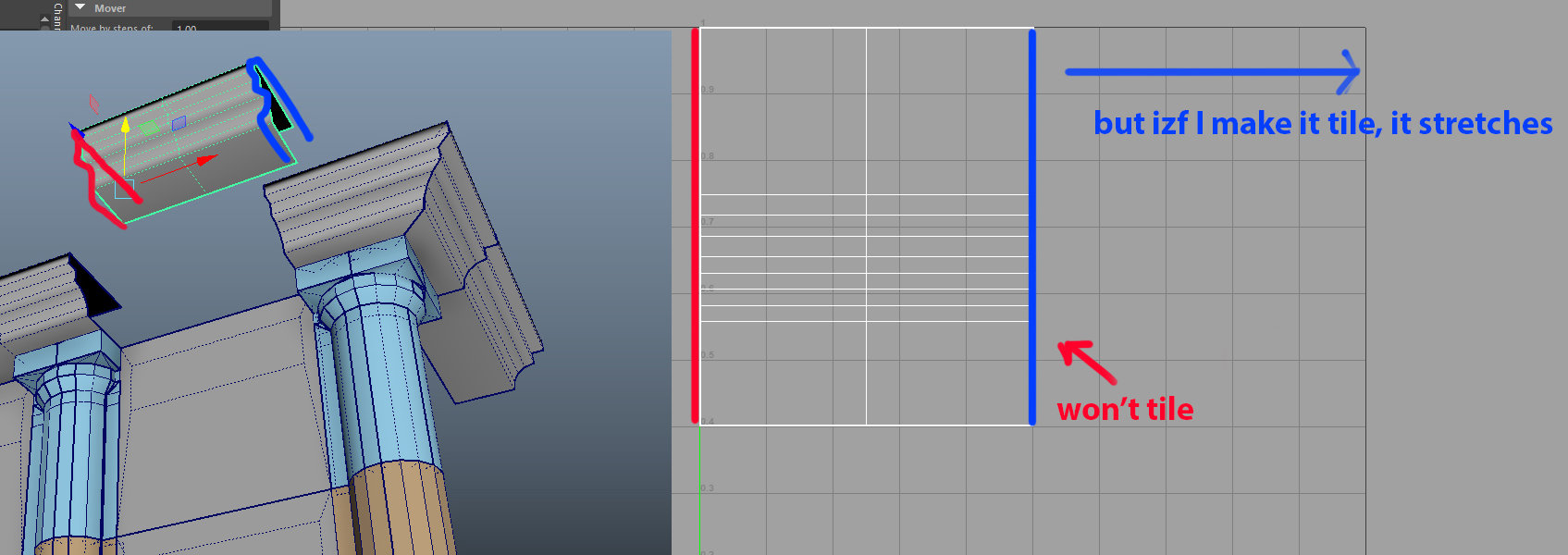
Any advice would help me enormously.
Also, if anyone suggests that its fine to have a seam at the corner, I know that is ok sometimes. I'm asking this because I need to know what to do when a seam doesn't belong at the corner...like in my current situation.
Replies
Think of your trim sheet as a never ending strip of normal map(or material), when you have an UV island that would extend beyond the 0-1 space its just going to be more of your same tiling endless strip.
The seam at the overhang corner is not a problem honestly, there should be seams however on what would be the top and bottom of that piece to allow for those faces to be scaled up to fit the tiling material. Basically the space within the green box should be its own island and scaled matching your kit's texel density. Example being if that is a 1m portion it could take up a 1k map so the part where the island is past that 1m mark would hang out of the 0-1 UV space. (Blue line on the UVs below)
Edit: In regards to the second image, this applies to pieces like walls where you would be butting one next to the other and needing a material tile properly across the surface as whole. If there are no seams in your trim sheet it will continue on tiling regardless of your UV space.
the 2m piece tiles with the corner on top. And the 4m piece tiles with the corner in the 2nd image, but do I really have to change the UVs on every corner piece depending on the situation?