Hey guys, I still have a lot to learn when it comes to hard-surface modeling. I was wondering what would be best way to approach adding vents on a curved metal surface?
Right now, I've separated the vent detail portion from the main mesh (screenshot below) The vents are not uniform and follow the surface bend.
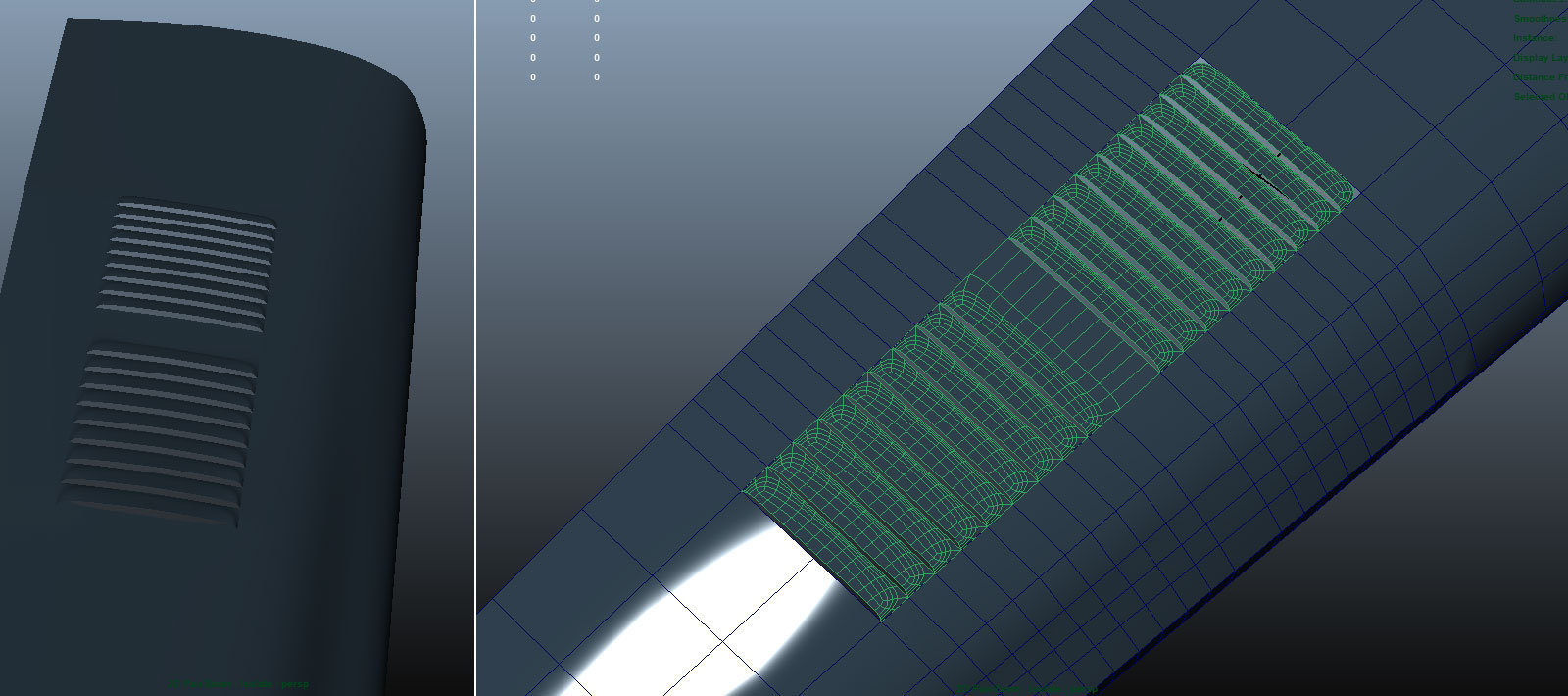
Next step, I added some fencing edges and tried to clean up the mesh, but the smooth mesh still has some pretty bad pinching (I'm sure there is a better way of redirecting the edge flow to avoid this, and I'll give it another shot)
As a general workflow rule, I keep my meshes fairly low-poly and use the smooth mesh preview to visualize the result. In this case, I'm not too concerned about the polycount and I just want to achieve a production level topology. I would like to add vents on much more curved areas like so:
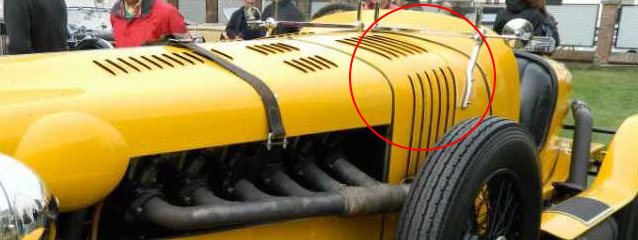
Looking forward to ideas, thanks!
Replies
1. keep it simple and make it clean flat
2. once it works correctly on one vent, flat, duplicate.
3. Finish most of the panel
4. Subdivide at least once and bend it.
I wouldn't work on it after it's bend, it's counter productive and a pain in the but.