Hi all
So, maybe there is an easy way to go about what I'm trying to accomplish but so far everything I've tried seems to lead to its own set of problems, and I was hoping some kind soul on here could help me out

I'm trying to prepare a mesh for 3d printing. The issue is, the original mesh is multiple subtools, and I have been told that in order to 3d print, it needs to be a single uninterrupted mesh. Not sure why, haven't looked more into that, so if that base assumption is wrong... *shrug* maybe I don't need to do all this lol.
But assuming I do: the issue is one of mesh clarity and crispness.
I've tried these things both with and without running Decimation Master first but I run into the same problems, so I went with 'after decimation', as it's obviously easier for my pc to handle quickly.
1. If I use Zremesher, everything turns into a low-poly blob and I lose all my detail. Doesnt seem to matter which options I use... I have yet to try reprojecting detail over and over because the bizzare geometry I seem to get from DM seems to screw it up.
2. If I use Dynamesh I get these weird 'merges' between subtools. With or without Project details I get them, although they are fewer with Project on (but more noticable...see image).
I'm not sure what to do at this point. COULD I theoretically re-sculpt all the hard edge divisions after dynameshing? Sure...but that's gonna take a ton of time that I don't know how to do easily, or guarantee it would look good. And then wouldn't I have to dynamesh again at the end to clean it all up, thus causing more of the same?

Please help

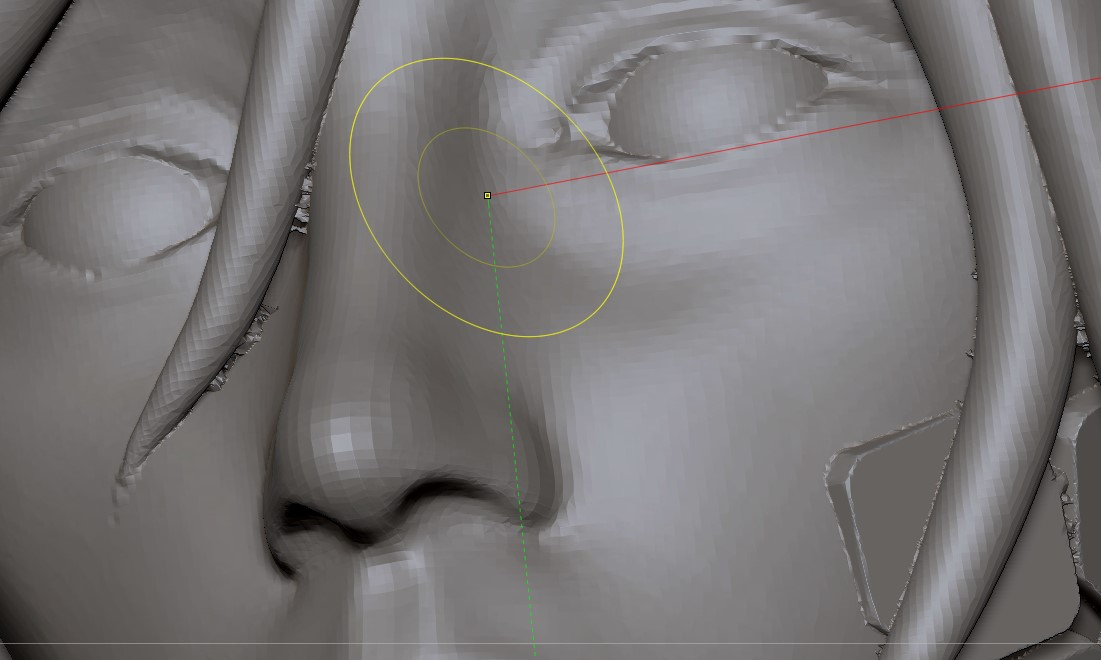
Replies
Alright, I will have to play with the dyna resolution.
This one is very small scale and so doesn't need to be hollow, and in fact being hollow would be bad I think, but I think you are right that it needs to all be one piece...
That's your problem right there. Only trust the specifications given by the people who will actually, practically print your model. Ironically this also applies to my own remarks below.
Models need to be watertight, for sure. But other than that, there are definitely path calculation methods that can deal with models with interpenetrating elements. Also, the people that you hire to print your model may be able to make some adjustments to your model themselves. Or may not. It depends.
So basically my overall recommendation is : do not assume anything, and work closely with the people who will actually print your stuff.
it does also create support geo...
The mesh is watertight, and I've used IMM stuff to close off all the tiny holes, but the creases/corners still give me trouble if I try to dynamesh.
So far I've been unable to get a nice clean transition no matter what I do. On the verge of giving up it occured to me: is there a way to like, copy the outermost mesh surface to a new subtool? Something like Unified Skin but higher res? If I could do that I'd be set. It's really just the way dynamesh/zremesher/etc wants to recalculate stuff that screws it up.
At the risk of sounding like a broken record, I'll reiterate : I'd recommend to contact the printing company right away, explain your project, ask them all the questions you have, and listen to what they are saying. You'll very likely be exchanging samples with them (they might show you/send you tiny test prints for you to check, and you could send them some test files for them test out). Every shop is different - some are very used to dealing with artists, some are not. Some may be able to process the sculpt for you, some may not.
"I've used IMM stuff to close off all the tiny holes, but the creases/corners still give me trouble if I try to dynamesh."
Ina way this is a bit of an issue too. You have to think less in terms of Zbrush-jargon, and more in plain 3d terms. It goes back to the above - some printing shops might be used to dealing with Zbrush models (and might even ask you for your ZTL, in order to save time if they feel like they can prepare the model faster than you would), while other might not. And so on
Now don't get my wrong, my point is not to say "this is the wrong way to do it, do it this way instead, it will be perfect". My point is more about the importance of clearly understanding the specifications of the shop you will be working with, in the interest of not wasting anyone's time.
Also : when people mention that the mesh needs to be watertight, they don't mean it in the sense of "plug these holes with more tiny meshes". They mean, really watertight, at the mesh level. When you create a sphere in a regular 3d program and then delete a face from it, you get a non-watertight mesh. This is often the only thing to avoid when dealing with 3d printing.
Good luck !