So I've been following Isaac Oster's f360 tutorials, and I really like the software. I'm able to get complex geo done in minutes which would take me hours otherwise. But when I export my mesh as STL or OBJ via converting solid body to a mesh, it triangulates everything. These tris are stretched and cause artifacting in my bakes. The tris in question are specifically concentrated around areas where planes meet curved surfaces, or where f360 welds edges on a plane to support geometry that's been cut into a face.
It looks as though it's setting some edges as hard, and others as soft, and causing these issues in the high poly normals. Setting the mesh to hard edges solves some issues on planes, but does not solve the issue where planes meet bevels/fillets.
How are you guys baking these high polys? Have you had these issues? What did you do to solve them? I've been bringing them into zbrush and dynameshing with dynamesh master, but that's duct tape on a problem that needs to actually be resolved. Furthermore, Zbrush crashes when working on more complex shapes. I will need to break the parts up and dynamesh them separately, which will create panel lines where I didn't necessarily want them.

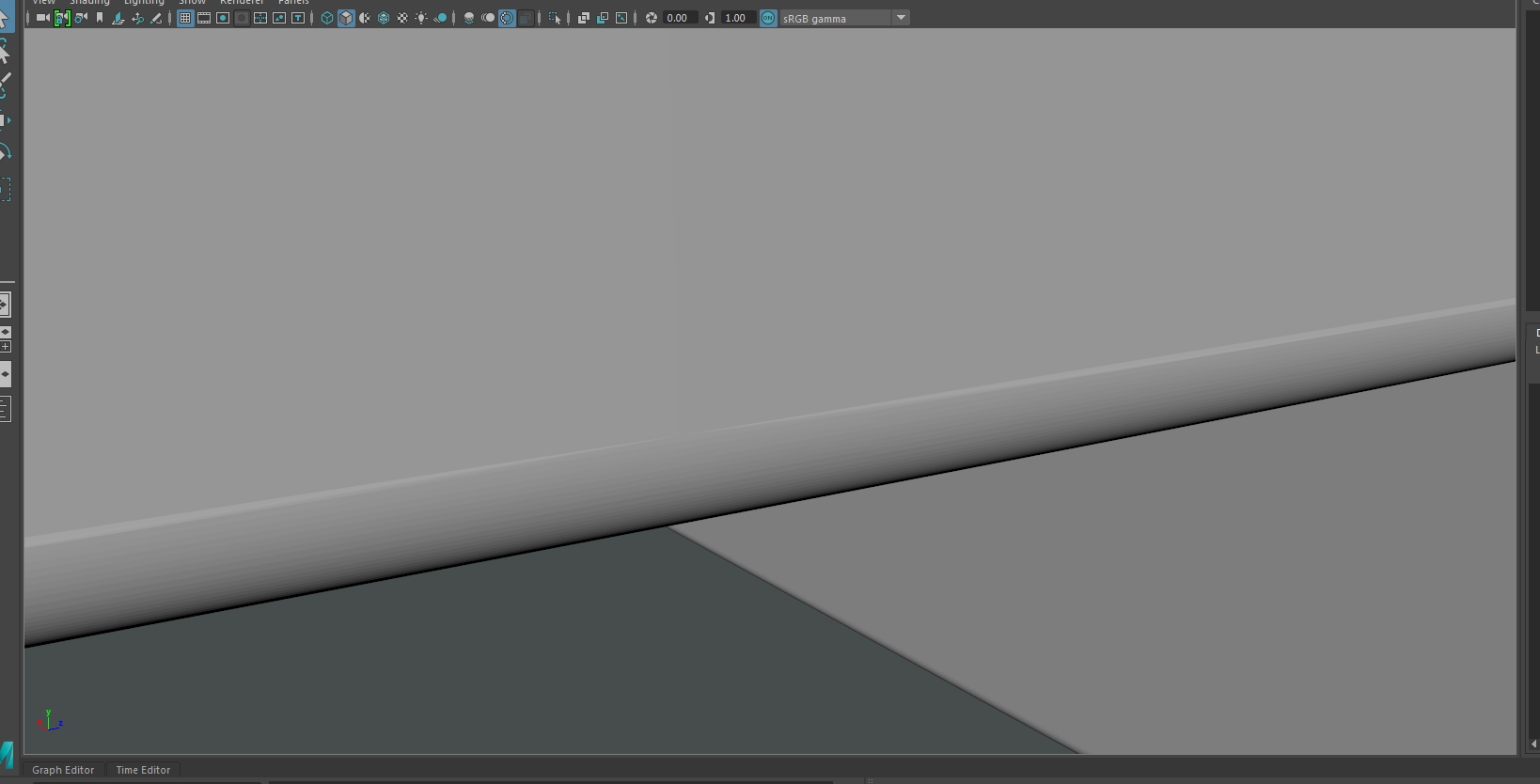
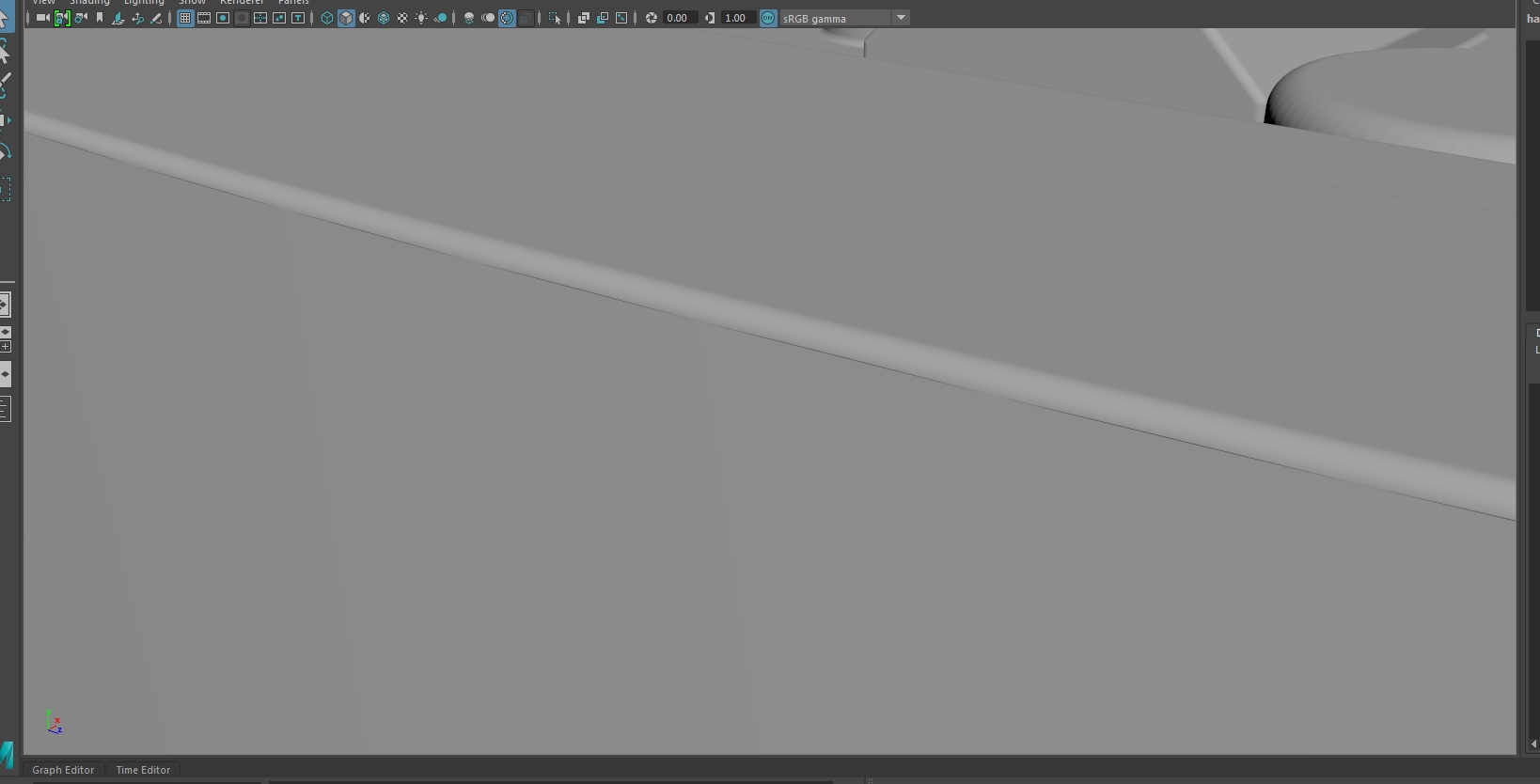
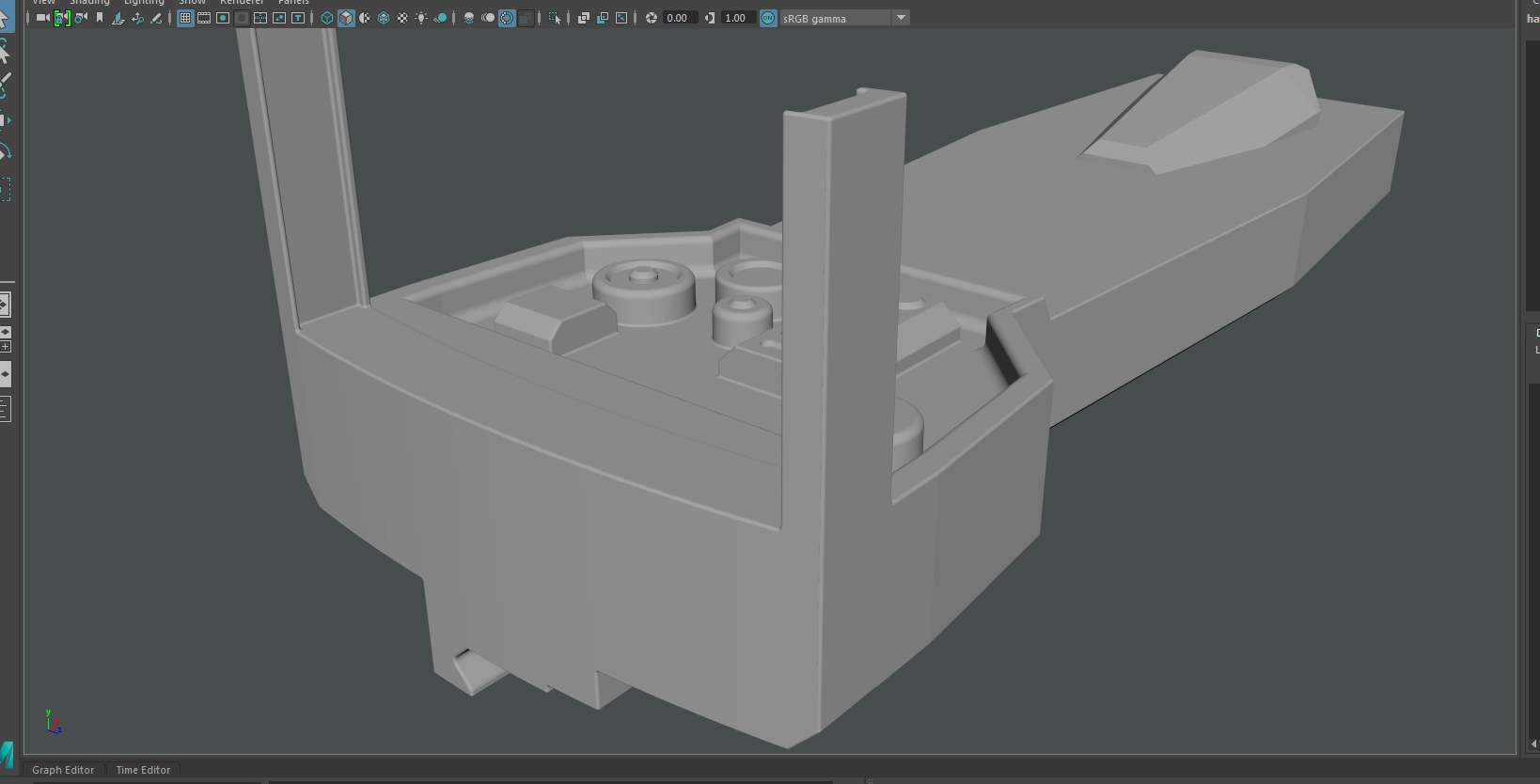
It looks OK from far away, but when I bake, these broken normals REALLY like to show up in map, so there's no hiding it.
Replies
omg you're right. The export box was truncated and I didn't see it. Testing now!
I don't have any more problems except on this kind of shapes. How I could to do ?