Hey guys, so I was thinking of making my first 3d print from one of the busts I made and I had some questions I wish someone with some experience in the matter could answer.
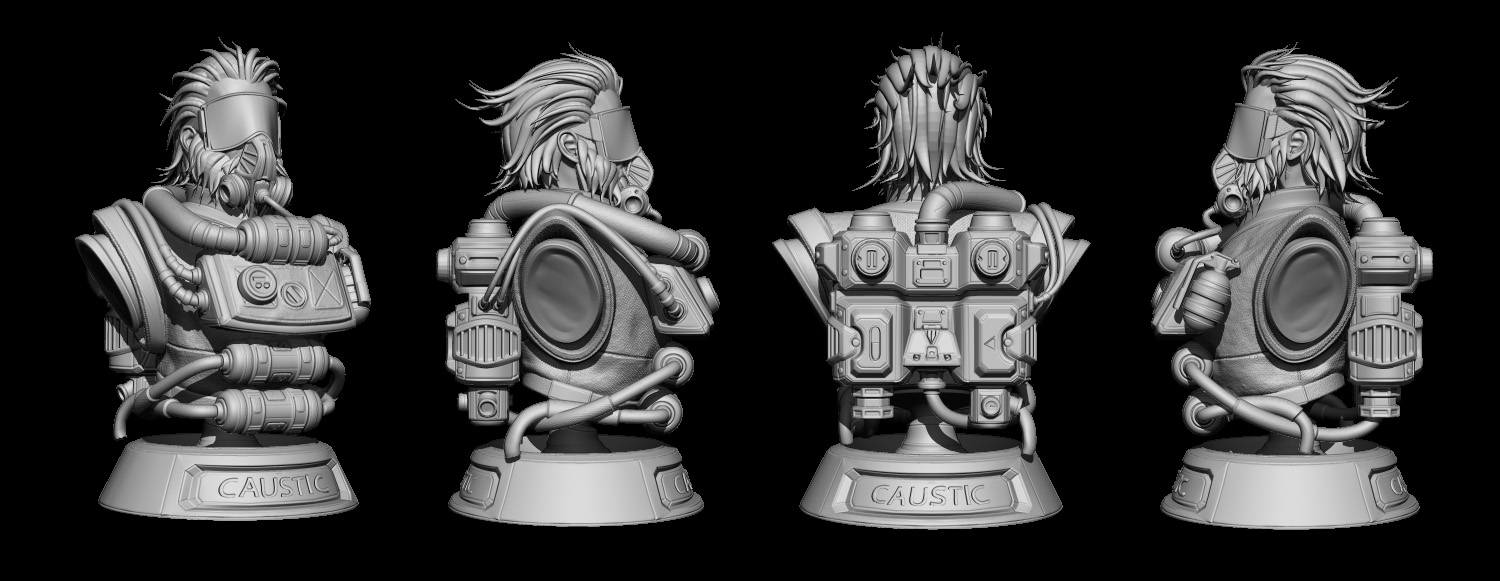
1. So from what I know the meshes have to be completely sealed up, but I was wondering if it's necesary to Dynamesh everything together like the screws, the tubes and the belt for example to avoid clipping or I can just ignore that.
2. How should I go about making the hair and beard? I'll probably Dynamesh them later and make them a bit thicker in some parts so it doesn't break, but will the printer be able to manage so many slopes? From another thread I read on Polycount pieces with that many slopes tend to give problems.
3. How should I cut the model? Since there are tubes connecting the part of the bag with the backpack I'm not sure how I could slice that into pieces to then stick it all together.
4. My idea was to print the glass of the glasses actual glass so you could see his eyes, but for that I would have to make it a separate piece and then stick it to the glasses. Would that be posible for something so thin or should I just give up that idea? I'm planning to make the print 45 mm tall.
Thanks for any help.
Replies
https://ultimaker.com/en/products/ultimaker-cura-software
1. I'd say you can avoid that, and it's more that you shouldn't have any open holes in your model rather than needing to sew everything together. You can still work with separate meshes as long as they're combined at the end to print.
2. Yeah, those sloes and thin tips will be difficult. Not really sure how to do that myself. It'll probably print okay but the tips will snap off easily. If this is just a one-off project, what if you sculpted the hair in some sort of clay (super sculpy etc) after printing and added it on there? This would be pretty easy to do in clay with little tubes.
3. The above poster has a good suggestion for slicing the model. But one other thing you'll want to consider is the direction you'll be printing this in, and if you want to print separate pieces. Printing separate pieces will allow you to do different orientations for different parts which can have better print quality. You will also want to print things in a way that uses as few supports as possible, since those often lead to gross looking areas when you cut them off.
For example, I modeled and printed this tiny Zarya gun for my gf for her birthday. I didn't have time to finish the pieces as well as I'd wanted to (sanding/priming them more etc to fill in layer lines) but it turned out okay. Here's how I broke up the pieces, if I recall correctly, and why I chose to do them that way:
4. Again, if this is a one-off piece I would just use some sort of clear plastic and cut it to shape and then glue it to the back of the 3D printed goggle frame. I did another 3D print of Tracer from Overwatch and was considering this (ended up just painting in the goggles orange though). 3D printing glass is not really a commercially available thing afaik.
Also, printing this with a nice level of detal at 45mm tall (a little under 2" it seems) will require a pretty nice printer, especially if you want to get the fine details on the gears/knobs on his kit. Are you planning to send this off to Shapeways etc to get it printed?
So this is how I would slice the model and the arrows are the directions the pieces would be printed from.
So my idea is to make the glass by hand with some small piece of plastic or glass.
My biggest problem right now is the gray piece with all those tubes, because since some of them are too small to be printed as separate pieces and then stuck together I think maybe the best way to do it is printing it all in one part from the backpack to the bag (the grenade is grey too).
I want to know what you think about this, also considering the small tube of the mouth that could complicate things.
Maybe making the head, the beard and the mask a single piece and printing it from the head to the neck would be a better option too?
@Carabiner Thanks a lot for the tips and the breakdown, really useful!
I don't have a printer, so my idea was to use Shapeways, yeah.
So according to what you say in the first tip, could I let the tubes open like this:
...if they are clipping with the rest of the pieces in a way that the hole is not "accessible"? I ask this because I can't change the topology without having to remove the subdivisions of the sculpture and it would be a bit of a pain in the ass.
Edit: Btw I messed up with the units of measure for the print, I was thinking more of 15cm (150mm, 5.9 inches), not 45mm.
Even with a resin printer like the Form One im not sure if it will work.
~6" is a bit more do-able than 2". The hair pieces will still be tricky though.
The gray piece with all the tubes might not print very well. Printing cylinders like that on an angle is not going to create a greaaaat result, but it might be fine depending on the fidelity of the printer/nozzle. Can you send it off for a test print before you continue too far with modeling? If you separated the main tube piece from the body, that would help too (so you don't need supports for the parts that are slightly floating).
In the end I didn't bother with the wall thickness for this case, so I hope it doesn't waste too much material.
Here are the pieces:
And this is how they are oriented inside of Zbrush to be exported as one STL file to Shapeways from what I've seen on Youtube:
What do you think? I've tried not to slice too many pieces at the end to make things more manageable. Do you find anything weird or that could complicate the printing? The model should still be about 150mm tall even if is rotated to be printed in one go.